Slurry pumping is a critical process in various industrial applications, such as mining, dredging, chemical processing, and wastewater treatment. Choosing the right pump for slurry can be challenging due to the abrasive nature of the particles and the varying consistencies of the mixtures. Here's a comprehensive guide to understanding which pump might be most suitable for handling slurry, based on real-world experiences, expertise, and authoritative insights.
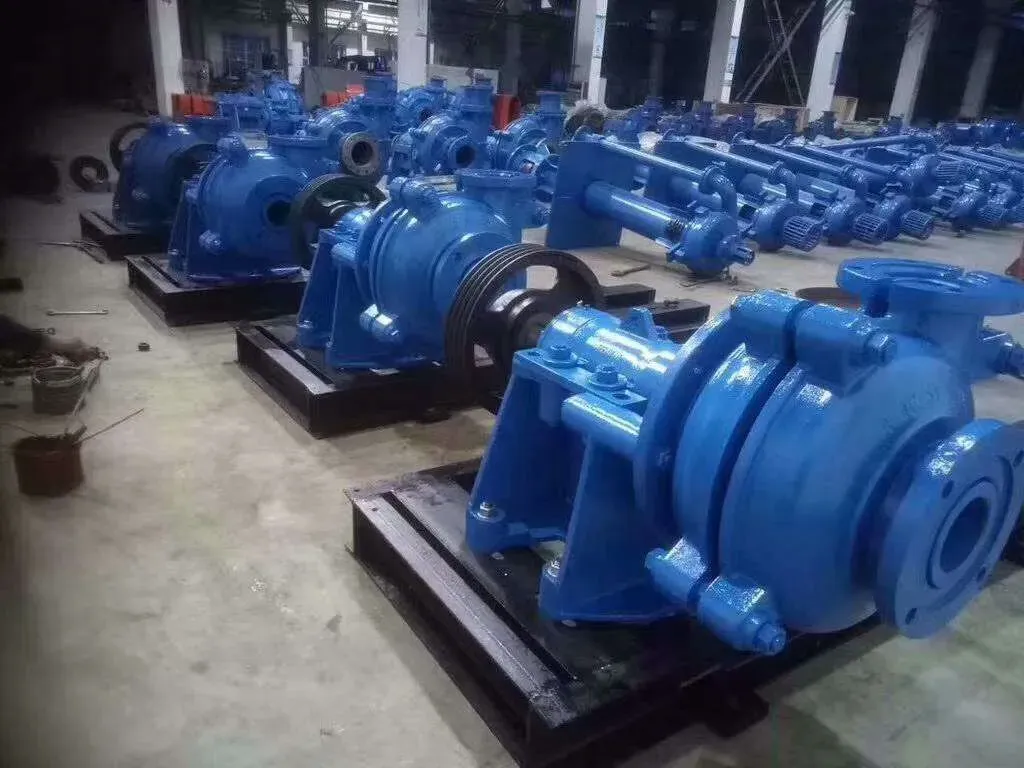
When dealing with slurry, one must first grasp the nature of the material being pumped. Slurry is essentially a mixture containing solids suspended in liquid. These solids can range from fine particles to large, abrasive materials. The concentration of these solids impacts the selection of the pump, as higher concentrations require more robust designs.
Centrifugal pumps are the most common choice for handling slurry due to their ability to handle high flow rates and their durability when dealing with abrasive materials.
These pumps operate by converting rotational kinetic energy into hydrodynamic energy to move the slurry. Thanks to their open impeller design, centrifugal pumps maintain efficacy even with viscous and dense slurries containing large particles. They are particularly suited for scenarios where maintaining a continuous flow is essential.
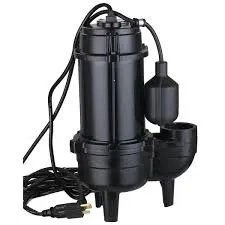
An expert from the mining industry, with over two decades of experience, states that centrifugal slurry pumps are preferred in mining operations for their robustness and low maintenance needs. The heavy-duty construction, often using materials like high-chrome or rubber linings, ensures they withstand the harsh conditions typical in these environments.
Positive displacement pumps, encompassing peristaltic and diaphragm pumps, also play a significant role in slurry applications, particularly when precision and control over flow rate are required. These pumps are ideal for situations where the slurry must be moved at lower velocities to preserve the integrity of delicate materials or to prevent excessive wear on equipment.
A chemical engineer with extensive experience in waste processing underscores that diaphragm pumps are particularly advantageous for handling slurries with variable viscosities and pressures. Their ability to create a sealed environment can prevent leakage, making them suitable for handling toxic or hazardous substances. They are also known for their energy efficiency and adaptability to different operational conditions.
which pump is used for slurry
Peristaltic pumps, characterized by their flexible operation and low maintenance, are useful for transporting thick slurries with high solid content. Since the slurry does not come into contact with mechanical parts, the risk of wear is significantly reduced, thus extending the pump’s lifespan. An authority in wastewater treatment highlights the role of peristaltic pumps in achieving precise dosing and reduced downtime, enhancing operational efficiency.
Often overlooked but equally important are submersible slurry pumps, particularly in dredging or underwater excavation projects. These pumps are versatile and can handle various slurry consistencies directly from the source. Their design allows for direct contact with the slurry, minimizing the need for complex piping systems and maximizing suction capabilities.
Trust in the equipment’s capability is most often derived from field success and user testimonials. All pumps mentioned have proven track records in diverse real-world applications, with outcomes documented in case studies across industrial sectors. For instance, a leading manufacturer of submersible pumps notes a significant increase in productivity in large-scale dredging operations, attributing success to the pump’s reliability and adaptability to challenging underwater conditions.
Choosing the right pump for slurry is thus a balance between understanding the properties of the slurry, the desired flow rate, pressure requirements, and environmental conditions. Consulting with engineers who specialize in fluid dynamics and industry-specific applications can provide additional guidance, reinforcing trust in the decision-making process.
Ultimately, the right pump configuration ensures not only operational efficiency but also long-term sustainability of the infrastructure. By leveraging expertise and authoritative insights across industries, one can select a pump solution tailored to meet specific requirements, enhancing both performance and profitability.