Understanding the intricacies of a double diaphragm pump's suction lift is vital for industries relying on fluid transfer systems. These pumps, renowned for their versatility and efficiency, are integral to sectors ranging from chemical processing to wastewater management. However, optimizing their suction lift capabilities requires a blend of practical experience, technical expertise, and authoritative insights—all underpinned by trustworthy data.
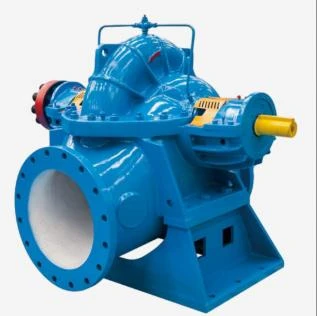
Experience Real-World Insights into Suction Lift Challenges
In practice, maximizing the suction lift of a double diaphragm pump can present challenges that vary based on environmental and operational conditions. Operators often encounter issues such as cavitation or air entrapment, which can impede performance and lead to costly downtime. For instance, in a chemical plant scenario, maintaining optimal slurry flow rates demands constant vigilance to avoid friction losses and blockage within the system. Experienced technicians emphasize the importance of regular maintenance and periodical checks of the diaphragm integrity to prevent unplanned pump failures and optimize suction lift.
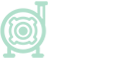
Expertise Technical Know-How in Pump Mechanics
Understanding the technical aspects of a double diaphragm pump's operation is crucial. Suction lift—the vertical distance between the fluid surface and the pump center—determines the feasibility with which fluids can be moved. Technical experts advocate for selecting the right type of diaphragm material, as it greatly influences how well a pump can handle viscous fluids or those containing particulates. Nitrile or Teflon diaphragms, for example, can significantly affect the pump's suction capabilities by providing enhanced chemical resistance.
Moreover, factors like inlet pipe diameter and length can also affect suction lift efficiency. Ideally, the inlet piping should be as short and direct as possible to minimize friction loss. Experts recommend using a foot valve in the piping to prevent the backflow of fluids, which can improve suction capacity and operational stability.
Authoritativeness Industry Standards and Guidelines
double diaphragm pump suction lift
Conforming to industry standards is critical for any organization deploying these pumps. Recognized bodies such as the Hydraulic Institute offer guidelines on pump installation and operation that, if adhered to, can enhance the suction lift capacity while ensuring safety and compliance. Training programs provided by pump manufacturers often contain authoritative recommendations, offering in-depth knowledge on handling specific models and optimizing their performance.
Documentation from such authoritative sources provides valuable checklists and protocols that maintenance teams can use to optimize their pump operations, ensuring they remain consistent with industry best practices. This authoritative backing thus serves as a benchmark for operational reliability, which is essential for building organizational credibility.
Trustworthiness Reliable Data and Testing
Trustworthiness in pump performance is achieved through rigorous testing and validated data. Labs and testing facilities often conduct performance evaluations under various simulated conditions to ensure that double diaphragm pumps meet advertised suction lift specifications. These tests help in determining the optimal operational limits and provide users with confidence in the pump's consistent performance.
Users should seek out manufacturers who provide empirical data and test results certified by reputable third-party organizations. This level of transparency ensures that the pump in question can meet the demands of specific applications without the risk of unexpected failures.
In conclusion,
optimizing a double diaphragm pump's suction lift is not a one-size-fits-all endeavor. It requires a combination of hands-on experience, deep technical understanding, adherence to industry standards, and trust in well-documented data. By focusing on these core elements, industries can maximize the efficiency and reliability of their fluid handling systems, ensuring that they meet both operational needs and quality expectations.