Slurry transport using centrifugal pumps is a pivotal process in various industries, including mining, wastewater treatment, and construction. Centrifugal pumps offer an efficient and practical solution to the challenge of moving slurries—a mixture of solid particles suspended in a liquid—over long distances. Yet, without the right approach and expertise, such systems can face significant operational and maintenance challenges. Based on extensive experience and insights from industry experts, this article delves into the intricacies of centrifugal slurry pumps, offering detailed guidance for enhancing their effectiveness and longevity.
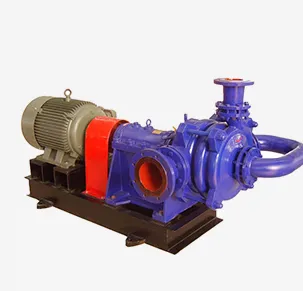
Understanding the Nature of Slurries
Slurries can vary widely in terms of particle size, concentration, and the nature of the carrying liquid. These variables significantly affect pump selection and system design. For instance, abrasive slurries with larger particles and higher concentrations pose a greater wear challenge to pump components. This requires careful selection of materials such as high-chrome iron or elastomers for pump construction to ensure durability.
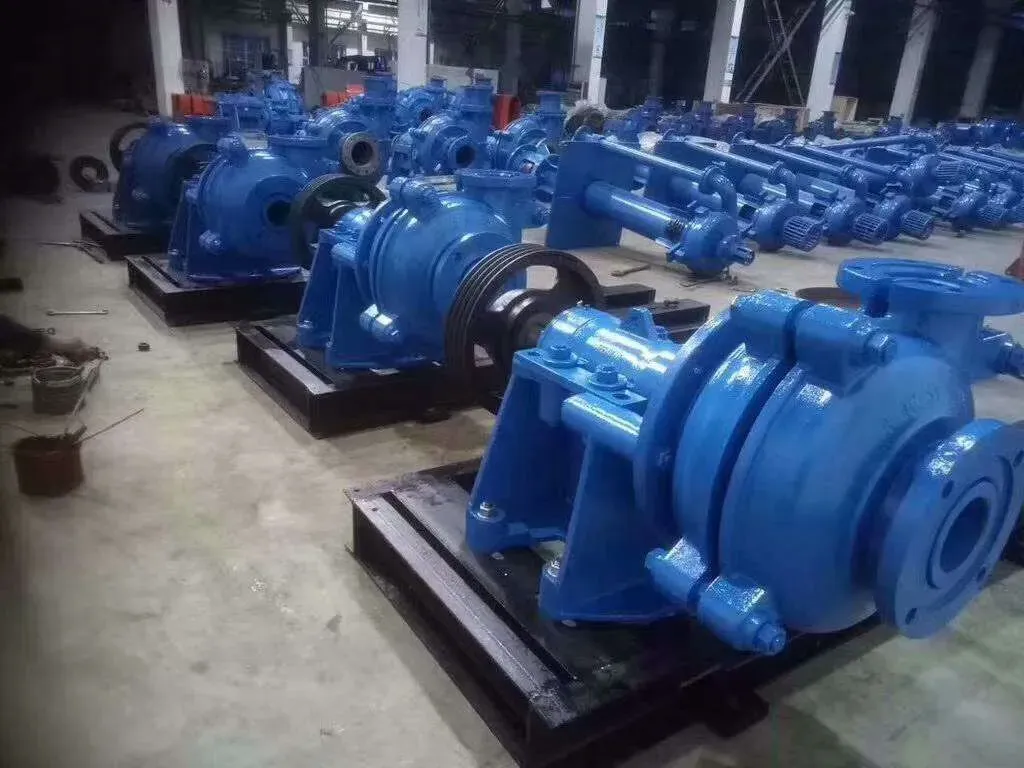
Key Considerations for Pump Design and Selection
The successful transport of slurry using centrifugal pumps hinges on several critical factors
1. Pump Selection Choose a pump that matches the slurry characteristics. Semi-open impellers are often preferred for handling slurries as they accommodate larger particles without clogging. Adjusting the impeller, volute, and casing materials can significantly extend pump life under abrasive conditions.
2. Impeller Design The impeller size and shape must efficiently handle the anticipated slurry flow while minimizing wear. Radial-flow impellers, for instance, are known for their ability to manage high-pressure requirements with minimal wear, ideal for large particle slurries.
3. Material Selection Wear-resistant materials reduce downtime and maintenance costs significantly. The choice of materials for the wear parts is dictated by the abrasion, corrosion, and pH levels of the slurry. Investing in high-quality materials pays off through prolonged service intervals.
4. Operational Parameters Avoiding operation near the pump’s best efficiency point (BEP) can accelerate component wear and energy consumption. Ensuring that the operation aligns with the manufacturer's guidelines mitigates unnecessary strain.
Maximizing Efficiency and Longevity
slurry transport using centrifugal pumps pdf
Operating a slurry pump efficiently is not just about choosing the right equipment—a comprehensive approach to system design and maintenance is crucial.
1. Regular Maintenance and Monitoring Implement a robust maintenance schedule that includes routine inspections and condition monitoring. Technologies such as vibration analysis and real-time monitoring via IoT can preemptively detect issues before they escalate into major failures.
2. Piping System Design Each bend or inclination in a pipeline can introduce head loss and increase the risk of blockage. Carefully designed pipelines with gradual curves and strategic placement of valves reduce energy losses and maintenance requirements.
3. Economic Considerations Consider the total cost of ownership (TCO) rather than just the initial investment. Analyzing the lifespan costs—from energy use and labor to part replacements—often justifies investing in a higher-quality pump initially.
4. Training and Expertise Development Continuous training for personnel ensures operational efficiency and safety. Keeping operators and maintenance personnel abreast with the latest technologies and methods optimizes both the performance and lifespan of the pump.
Advancements and Innovations
The field of slurry transport is evolving, driven by technological advancements and innovation. Emerging trends include smart pump systems equipped with sensors and automation capabilities that allow for real-time performance adjustments and predictive maintenance scheduling. These technologies enable more responsive and adaptive systems, reducing downtime and enhancing performance metrics.
A Sustainable Approach
Sustainability has become a critical focus in pump design and usage. Energy-efficient pump systems not only reduce operational costs but also minimize environmental impact. Manufacturers are increasingly designing pumps that leverage renewable energy sources and include eco-friendly materials to promote a circular economy.
Drawing from extensive field experience and technical expertise, slurry transport with centrifugal pumps remains a sophisticated balance between design, maintenance, and technological integration. As industries continue to demand more efficient and reliable solutions, embracing these insights fosters improved operational success and extends the functional life of pump systems, thereby reinforcing their pivotal role in industrial processes worldwide.