Understanding the intricacies of slurry pump calculations is crucial for businesses dealing with challenging fluid handling environments. Having amassed years of experience in this domain, I've encountered numerous situations where precision in calculations has drastically enhanced operational efficiency and reduced downtime.
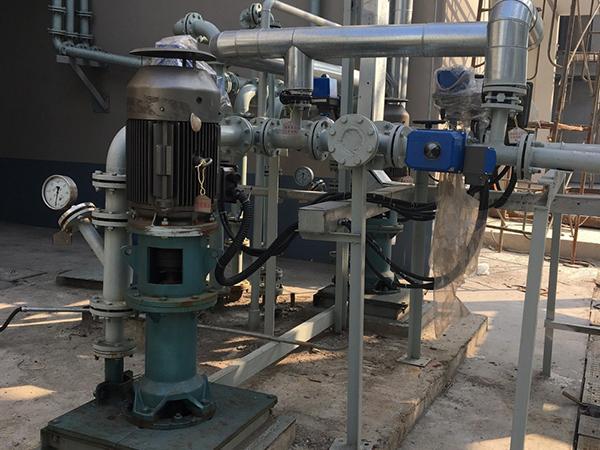
Slurry pumps are specialized equipment designed to handle abrasive and corrosive slurries found in mining, construction, and other heavy-duty sectors. An authentic understanding of their operation extends beyond basic function— requiring a deep dive into specific calculation parameters such as flow rate, slurry density, pump capacity, and power requirements.
The first critical calculation in optimizing a slurry pump’s performance is determining the flow rate, typically expressed in cubic meters per hour (m³/h). This measurement hinges on understanding the volume of solid-laden fluid the pump needs to move, which further informs decisions on pump size and power.
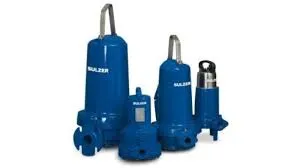
Next,
slurry density plays a pivotal role in calculations. This measure indicates the weight of the slurry relative to the volume it occupies, factoring in both the liquid and solid components. In practice, this means accurately assessing the percentage of solids within the liquid—a nuanced task that demands expertise and precision. Errors in density calculation can lead to pump wear, inefficiency, or even complete system failure.
slurry pump calculations
Calculating the pump capacity involves a detailed analysis that considers the pressure head required to transport the slurry over a specific distance and elevation. This is where understanding hydraulic principles becomes essential, as it informs the energy requirements and ensures the pump operates under optimal conditions. The Total Dynamic Head (TDH) is calculated, taking into account static head, friction loss, and velocity head, with each element requiring careful consideration to ensure optimal operation.
Power requirements further complicate the slurry pump equation, yet understanding them is fundamental to the system's overall energy efficiency. This involves calculating the brake horsepower (BHP) using the formula BHP = (Q x H x S) / (3960 x E), where Q is the flow rate, H is the total head, S is the specific gravity, and E is the pump efficiency. Meeting the power requirement accurately avoids undervaluing that could otherwise lead to insufficient pump performance or overvaluing causing energy wastage and excessive operational costs.
Safety and sustainability mustn't be overlooked within slurry operations—a perspective underscored by genuine experience. Ensuring accurate calculations not only improves operational efficiency but also contributes to extending equipment lifespan while minimizing environmental impact.
In conclusion, mastering slurry pump calculations is not merely a technical necessity but an embodiment of expertise and authoritative practice. Businesses can enhance their operational performance, safety standards, and environmental stewardship with precise computation and insightful application. True expertise and experience in this field bring trustworthiness—a cornerstone for any enterprise looking to optimize its industrial processes with slurry pumps.