The working principle of a slurry pump is a fascinating yet intricate process that involves the transportation of a mixture of solid particles and liquids. These pumps are essential in various industries, including mining, construction, and waste management, where the efficient movement of slurry—a thick, viscous fluid—is critical. Understanding the working mechanism of slurry pumps not only highlights their capabilities but also underscores their importance in optimizing industrial processes.
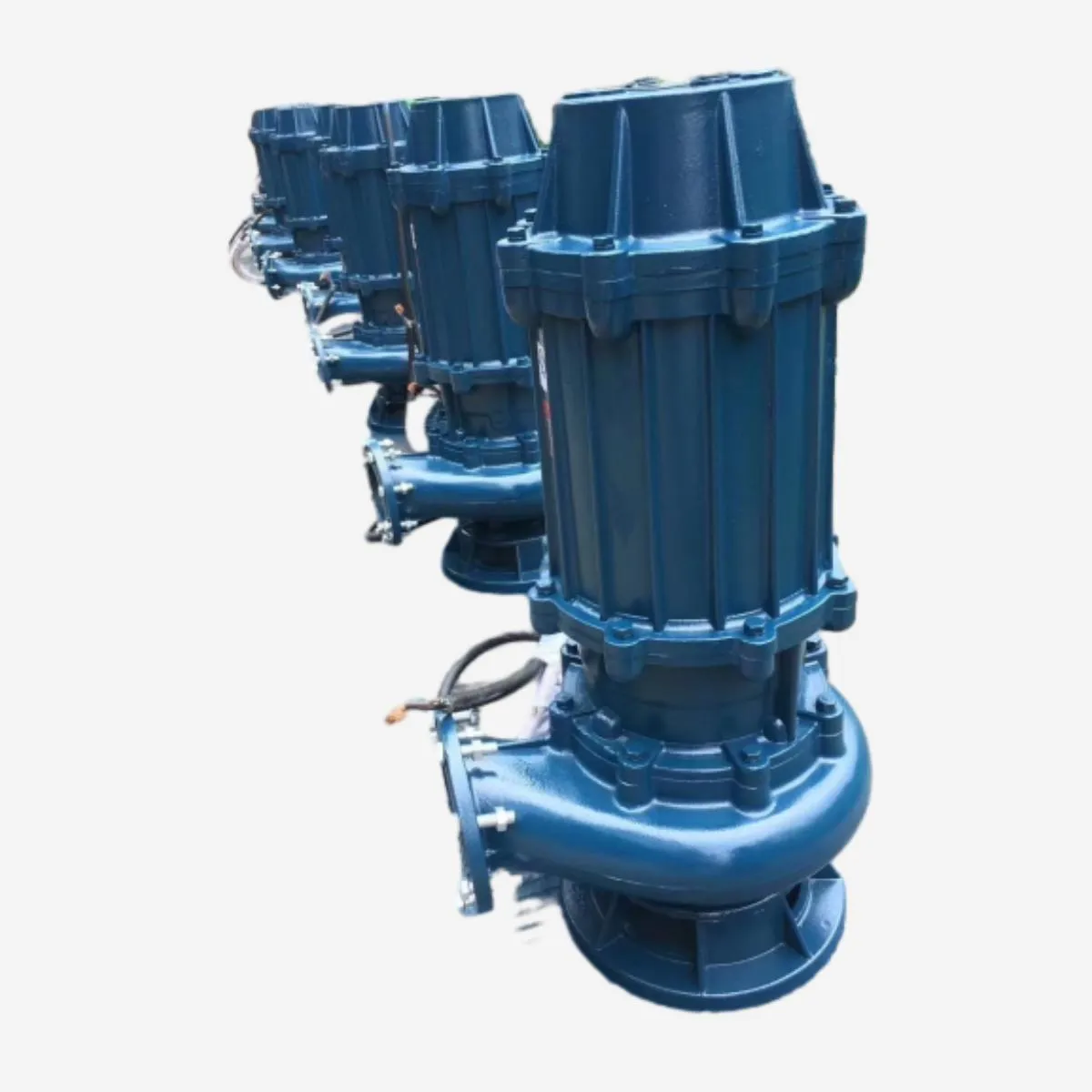
Slurry pumps operate based on the fundamental principles of centrifugal force. The core component is the impeller, which is rotated by a motor. As the impeller turns, it increases the velocity of the slurry. This velocity is converted into pressure energy, which enables the slurry to be pushed through the pump casing and pipework. The efficiency of this conversion process is paramount, as it determines the pump's ability to handle abrasive and corrosive materials commonly found in slurries.
Key to the principle of a slurry pump is the design and material of the impeller. To endure the harsh conditions of slurry pumping, the impeller is often made from high-chrome alloys or rubber. These materials are chosen for their resistance to wear and corrosion, ensuring the longest possible lifespan. The impeller is designed with vanes that are carefully engineered to manage the flow and minimize turbulence, reducing wear while maintaining efficiency.
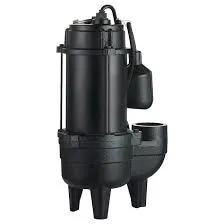
An understanding of the slurry pump's operational dynamics cannot ignore the significance of the volute casing—a critical feature that encircles the impeller. The role of the casing is to collect the pump discharge, converting kinetic energy from the impeller into a reduced velocity while increasing pressure. This conversion is crucial for directing the slurry efficiently through the pump system and into the discharge piping.
slurry pump working principle
In practice, there are several configurations of slurry pumps, including horizontal and vertical designs. Horizontal slurry pumps are often favored for applications where gravitational influence aids the flow, while vertical pumps are used where space constraints exist. The choice between these is often dictated by specific operational needs, including the nature of the slurry, the abrasiveness of particles, and the required head and flow rate.
A comprehensive understanding of the slurry pump working principle also involves acknowledging the significance of maintaining the pump's integrity through regular maintenance and monitoring. Bearing failure, seal failure, and lining wear are common issues that can degrade pump performance. Industry best practices suggest the implementation of predictive maintenance schedules, utilizing advanced diagnostic tools to pre-emptively address potential failures. This proactive approach not only prolongs the life of the pump but also maximizes operational uptime, which is critical in sectors where downtime equates to significant financial loss.
Furthermore, the adaptability of slurry pumps to various operational conditions highlights another dimension of their working principle. For instance, some modern pumps are equipped with variable speed drives, allowing operators to adjust the pump speed according to the specific requirements of the task at hand. This capability enhances efficiency, as the pump can be fine-tuned to use only the energy necessary to move the slurry at a given rate.
In conclusion, the working principle of a slurry pump is a testament to engineering ingenuity, balancing complex forces and materials to deliver efficient and reliable service in demanding environments. With advancements in technology and materials, the future of slurry pumps looks poised to offer even more sophisticated solutions, promising enhanced efficiency and reduced operational costs. For industries relying on robust slurry movement, investing in modern slurry pump systems is not just a necessity but a strategic move towards ensuring they remain competitive and capable in an ever-demanding market.