In the realm of fluid transport and management, slurry pumps play an indispensable role in moving thick, solid-laden mixtures across various industrial settings such as mining, mineral processing, and construction. One advanced method of optimizing the efficiency and reliability of slurry transport is by arranging slurry pumps in series. This technique, often overlooked, can significantly enhance pumping systems' performance, provided it is applied with expert precision and strategic insight.
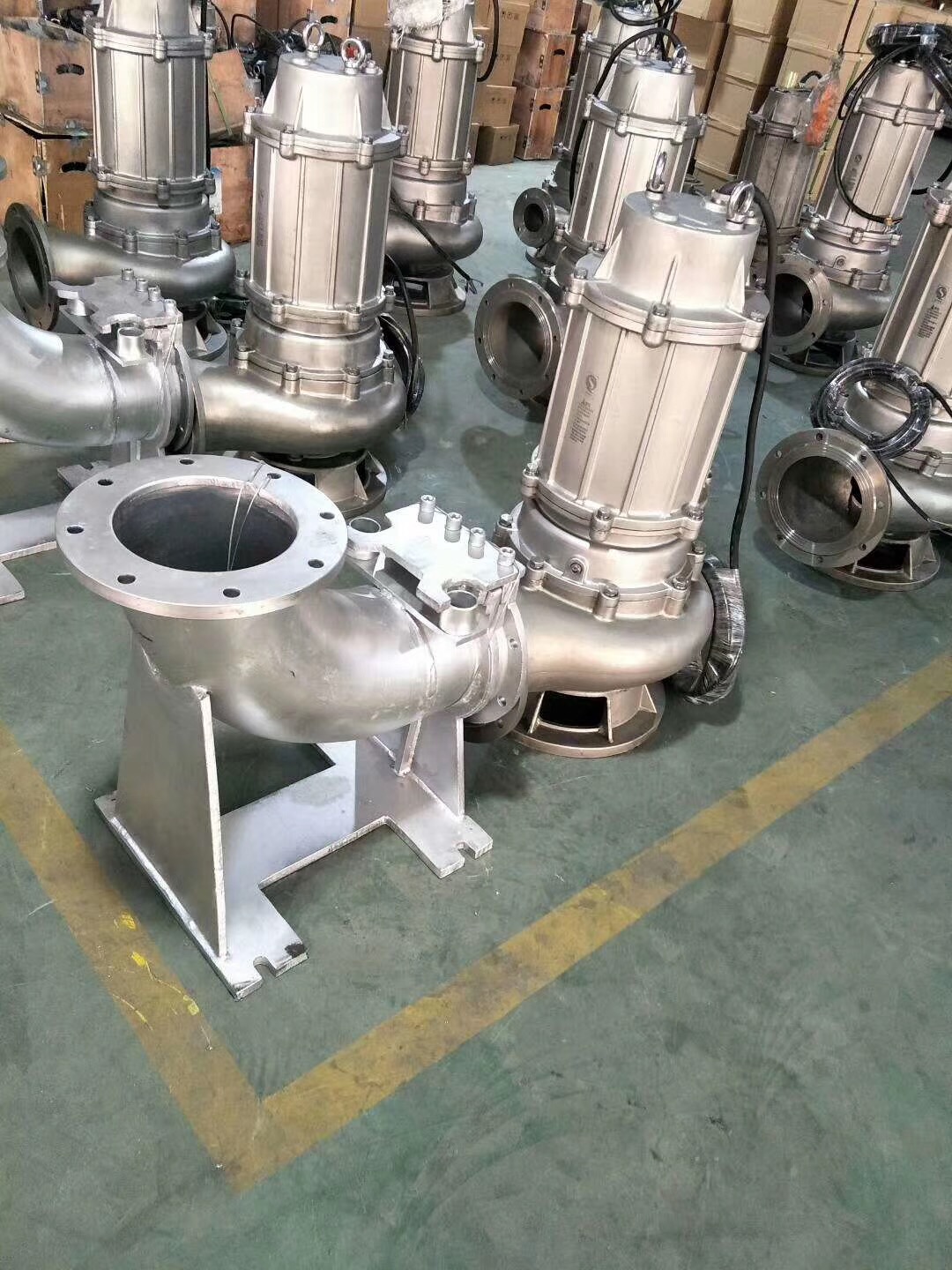
Arranging slurry pumps in series involves connecting multiple pumps along a pipeline such that the discharge of one pump feeds directly into the suction inlet of the next. This configuration can achieve a cumulative increase in head (the height to which a pump can lift fluid) without necessitating the purchase of a single, more powerful pump. This setup is particularly valuable when piping infrastructure spans significant distances or when it must overcome substantial vertical lifts, making it a preferred strategy in expansive mining operations and large-scale slurry processing plants.
The main advantage of deploying slurry pumps in series lies in their ability to maintain a stable flow rate against significant head loss over an extended distance. This continuity ensures that the slurry’s abrasiveness and corrosiveness are managed effectively, reducing wear on the equipment and minimizing downtime for maintenance. The continuity of flow achieved with series-configured pumps is critical in applications where constant and reliable operations are paramount to productivity, such as in mineral slurry pipelines.
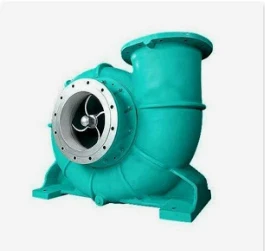
From an engineering standpoint, designing a series pumping system requires a thorough understanding of hydraulic principles and the specific characteristics of the slurry being transported. Each pump must be selected based on its compatibility with the slurry's particle size, density, and viscosity. Coupled with detailed calculations of the friction loss in the pipeline, engineers can configure a system that seamlessly integrates multiple pumps without exceeding the mechanical limits of each unit.
slurry pumps in series
In practice,
deploying pumps in series brings multifaceted benefits. As some industry veterans have observed, this configuration often results in improved energy efficiency due to optimized load distribution across the pumps. By operating closer to their best efficiency point, pumps in series can extend their operational life, further yielding cost savings and enhancing the sustainability of the operation. Moreover, in scenarios where a pump in a series system requires maintenance or inspection, the remaining pumps can often be configured to maintain partial operation, thereby avoiding complete shutdowns and ensuring continuous production.
However, planning and executing a slurry pump system in series is not without challenges. Expertise in selecting the right pump type is crucial, as centrifugal pumps, which are commonly used, may exhibit variable efficiency and wear rates depending on the slurry properties. Ongoing consultation with pump manufacturers and hydraulic consultants can provide actionable insights into the latest developments in wear-resistant materials and cutting-edge pump technologies that can further enhance system longevity and efficiency.
To foster trust and authority in implementing series pumping systems, it is advised to collaborate with established industry players and thought leaders who have made definitive strides in pump engineering solutions. Sharing successes and case studies through technical papers, webinars, and workshops can build credibility and promote the advancement of knowledge in this specialized field.
In summary, while the concept of arranging slurry pumps in series may seem straightforward, its successful execution requires a blend of technical acumen, strategic planning, and collaborative innovation. As industries continue to push the boundaries of what's possible with slurry transport technologies, leveraging the benefits of series pumping configurations will undoubtedly remain a key focus area for achieving operational excellence in an environmentally sustainable manner.