Slurry pumps are vital components in industries ranging from mining and mineral processing to wastewater treatment and beyond. These robust devices are engineered to handle a diverse array of challenging tasks, moving highly abrasive, viscous, and corrosive materials with efficiency and reliability. Based on years of industry experience, the effective selection and maintenance of slurry pumps significantly influence operational success, underscoring the critical role these pumps play in industrial operations.
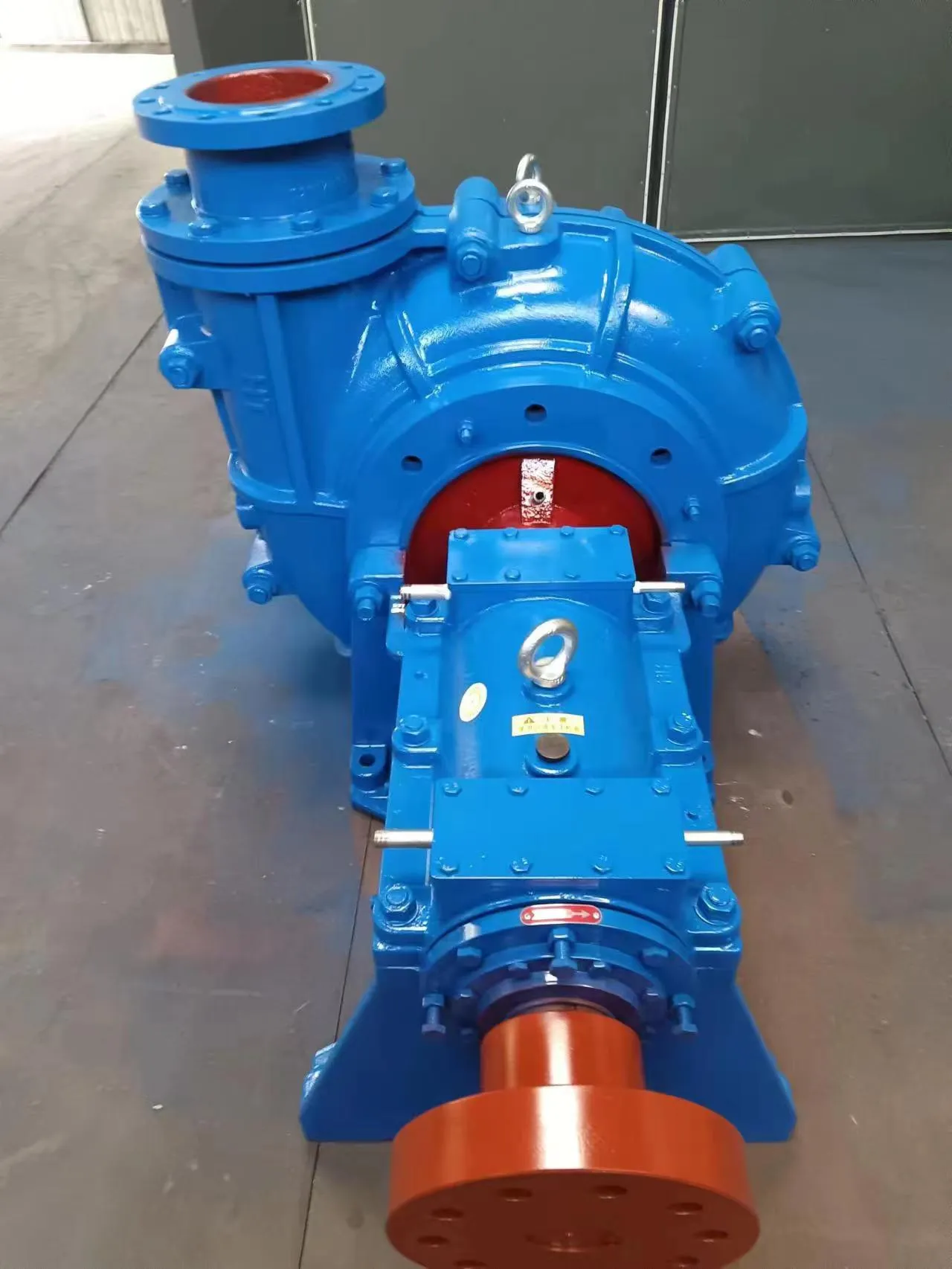
The expertise in slurry pump technology begins with understanding their design and operational principles. Slurry pumps are categorized primarily into centrifugal, positive displacement, and peristaltic variations, each tailored to specific types of slurry and operational demands. Centrifugal slurry pumps are often used in mining applications due to their ability to handle large volumes and oversized particles. Positive displacement pumps, on the other hand, excel in precise, high-pressure applications, making them ideal for transferring viscous slurries. Meanwhile, peristaltic pumps, with their seal-less design, are preferable for moving corrosive or toxic slurries without the risk of leakage.
Authoritativeness in this domain is built upon utilizing proven methodologies and technologies to improve pump efficiency. One key development is the use of wear-resistant materials such as rubber, polyurethane, and high-chrome alloys. These materials extend the lifespan of slurry pumps by resisting the abrasive nature of slurries, thereby reducing maintenance costs and downtime. Furthermore, advanced impeller designs have been engineered to optimize flow path and reduce movement-induced wear, enhancing durability and performance even further.
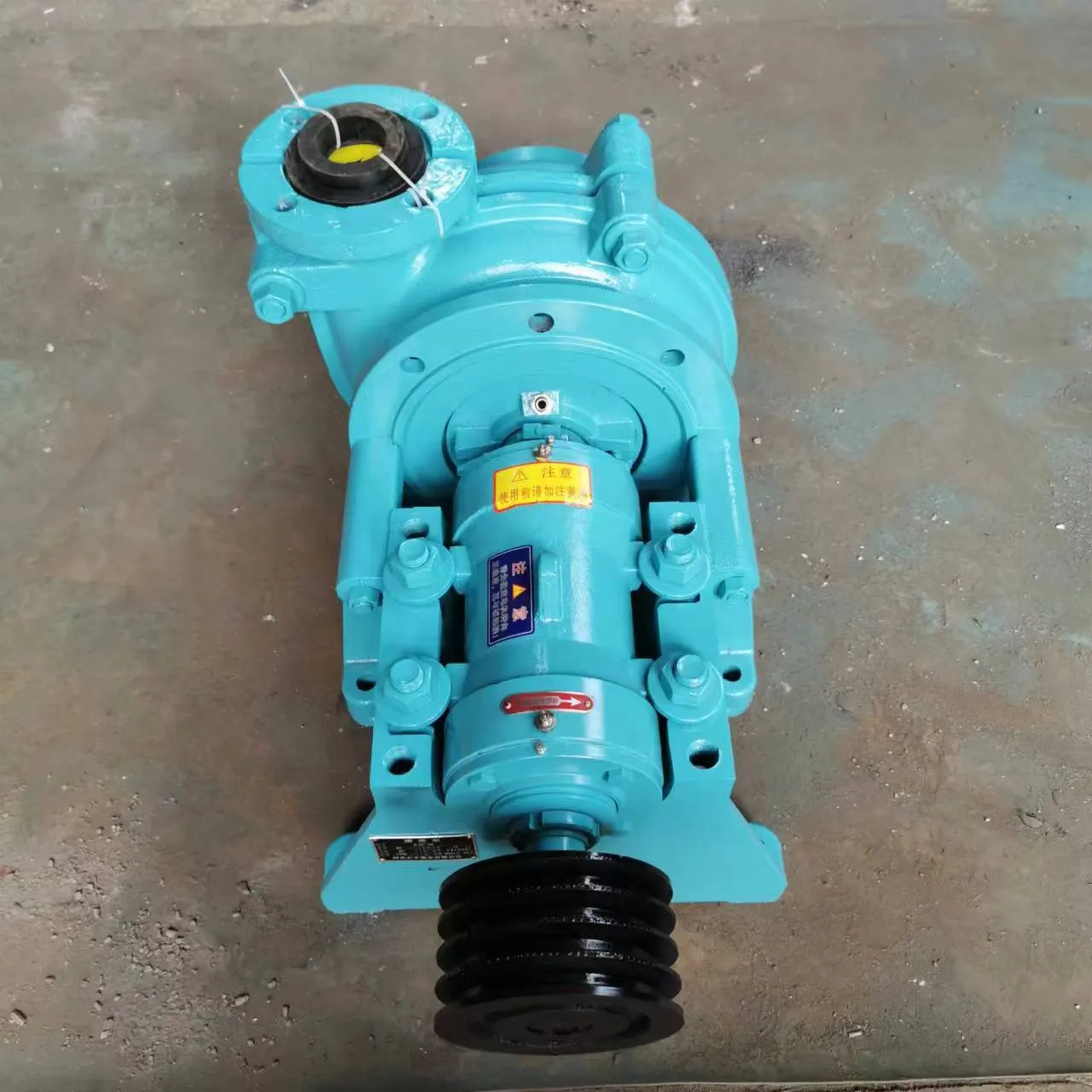
slurry pump
Trustworthiness in slurry pump deployment involves adhering to best practices in installation and operation. Ensuring proper alignment and secure mounting of pumps minimizes vibrations that can lead to mechanical failures. Furthermore, routine maintenance such as checking the seals, bearings, and flow passages for wear and tear is imperative for sustaining optimal operation. Real-world data analysis techniques can predict maintenance needs, allowing for preemptive repairs and replacements, which in turn prevents unscheduled downtimes and boosts operational efficiency.
In conclusion, the selection and maintenance of slurry pumps are paramount to industrial success. With advances in material science, design engineering, and predictive maintenance, pump reliability and performance can be continually enhanced. This ensures these critical systems operate at peak efficiency, supporting the complex and demanding environments they are deployed in. As industries continue to push for heightened productivity and efficiency, the next generation of slurry pumps is set to play an even more pivotal role. Leveraging expert knowledge to select and maintain the right slurry pump translates to sustained operational gains and long-term competitive advantage.