Slurry pumps are integral to various industries, renowned for their ability to handle abrasive and corrosive fluids with high solid content. For professionals seeking to optimize slurry pump performance, understanding the intricacies of their operation is crucial.
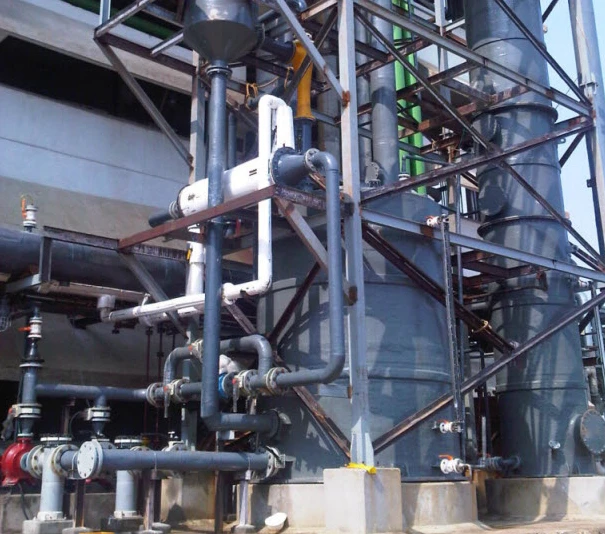
Slurry pumps operate based on the centrifugal force principle, utilizing rotating impellers to impart energy to the slurry, thereby moving it through pipelines or tanks. This robust machinery features several components designed to increase efficiency and durability under challenging conditions. The primary components include the casing, impeller, and drive shaft.
The casing serves as the outer shell of the pump, designed to contain the slurry and withstand its abrasive nature. Materials such as cast iron, high-chrome alloys, and rubber are typically used to enhance wear resistance. The impeller, a rotating disk with blades, plays a crucial role in transferring energy from the pump's motor to the slurry. Impellers need to be chosen based on the application's specific requirements, with open, semi-open, and closed designs being available. Each design has its advantages; for example, open impellers are more tolerant to larger solids, making them ideal for applications with varying particle sizes.
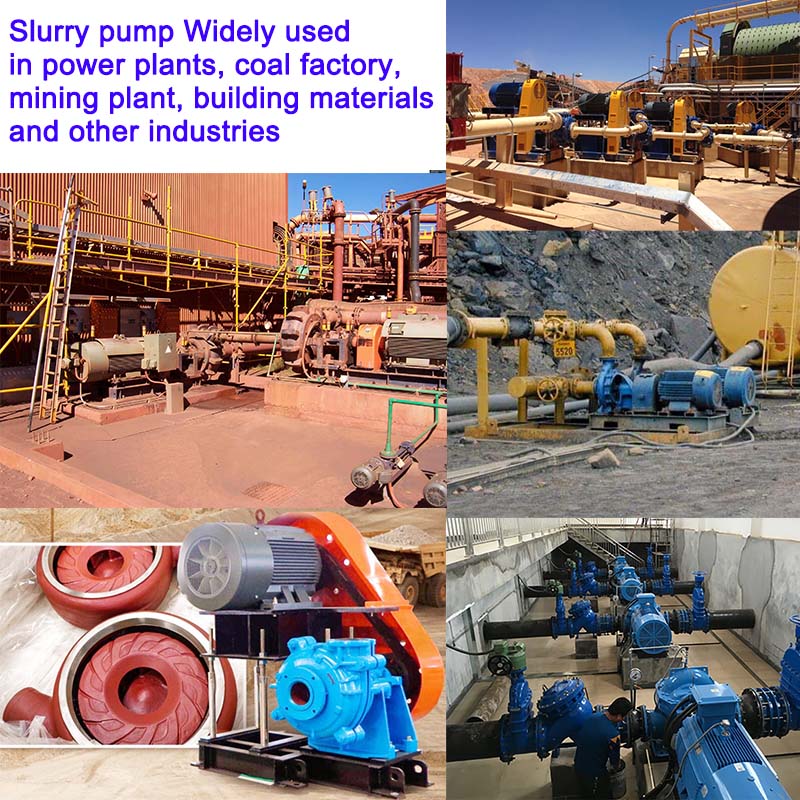
Drive shafts transmit the rotational motion from the motor to the impeller. In corrosive environments, selecting the right material for the drive shaft is essential to prevent deterioration. Stainless steel is often the material of choice due to its excellent resistance to corrosion and wear.
Essential to the slurry pump's operation is the understanding of how various factors affect its functionality. For instance, the size and density of the particles within the slurry directly influence the pump's efficiency and wear rate. High-density minerals or larger particulates require pumps with enhanced wear resistance and larger clearances.
Furthermore, the slurry's viscosity and pH level can impact pump performance and longevity.
slurry pump working
To ensure slurry pumps perform optimally, it is vital to carry out regular maintenance and monitoring. This involves routine checks for any signs of wear and tear, particularly in the impeller and casing, as these parts bear the brunt of the slurry's abrasive nature. Establishing a periodic maintenance schedule can preemptively address potential issues, thereby minimizing downtime and extending the pump's life.
Expertise in slurry pump systems also involves selecting the right pump design and configuration based on the specific industrial application. Industries ranging from mining, where slurry transportation is a daily necessity, to chemical processing plants, where handling corrosive materials is crucial, rely heavily on pumps tailored to their unique needs. Companies must work closely with trusted manufacturers to customize solutions that address their specific challenges, focusing on enhancing energy efficiency, reducing operational costs, and prolonging equipment life.
Adopting cutting-edge technologies and innovative design enhancements are critical strategies. Modern slurry pumps are increasingly featuring advanced materials and coatings to improve longevity and resistance to harsh environments. Moreover, integrating smart monitoring systems that provide real-time data on pump performance and condition is gaining traction, allowing operators to make informed decisions on maintenance and operations.
In summary, the effective operation of slurry pumps depends on a comprehensive understanding of their mechanics, a commitment to regular maintenance, and the strategic selection of pump types and materials tailored to specific applications. Industry professionals who grasp these elements and apply them conscientiously can achieve unparalleled efficiency and reliability from their slurry pump systems, ensuring they remain at the forefront of industrial advancements in fluid handling technology.