Chemical resistant pumps are specialized pumps that are specifically designed to handle and transport corrosive and abrasive fluids. These pumps are often used in industries where chemicals are a key part of the process, such as pharmaceutical, petrochemical, and food processing industries. The ability to resist the damaging effects of chemicals makes these pumps essential for the smooth and efficient operation of these industries.
One of the main reasons why chemical resistant pumps are important is because they help prevent damage to the pump itself. Corrosive fluids can quickly degrade traditional pumps, leading to leaks, malfunctions, and costly repairs. Chemical resistant pumps are made from materials such as stainless steel, plastic, or Teflon that are resistant to the corrosive effects of chemicals, ensuring that the pump remains in good working condition for longer periods of time.
Another key benefit of chemical resistant pumps is that they help ensure the safety of workers and the environment. Handling corrosive chemicals can be dangerous, as they can cause burns, respiratory issues, and other health problems if proper precautions are not taken. By using chemical resistant pumps, companies can minimize the risk of accidents and spills, protecting both employees and the surrounding environment.
In addition to their durability and safety benefits, chemical resistant pumps also offer superior performance. These pumps are designed to handle a wide range of corrosive fluids, from acids and solvents to abrasive slurries These pumps are designed to handle a wide range of corrosive fluids, from acids and solvents to abrasive slurries
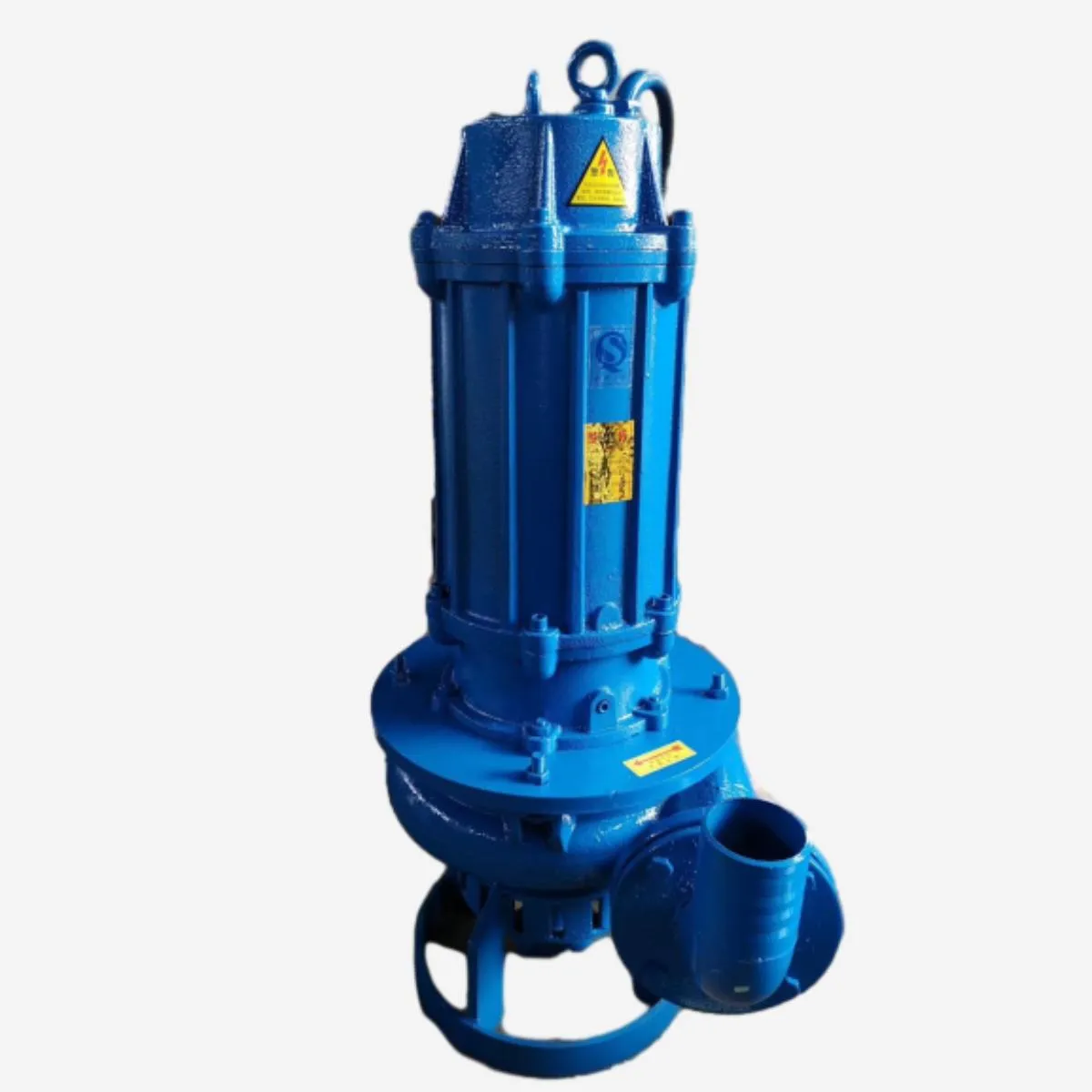
These pumps are designed to handle a wide range of corrosive fluids, from acids and solvents to abrasive slurries These pumps are designed to handle a wide range of corrosive fluids, from acids and solvents to abrasive slurries
chemical resistant pump. Their specialized construction allows them to maintain a consistent flow rate and pressure, even when dealing with challenging substances. This ensures that processes can run smoothly and efficiently, with minimal downtime or interruptions.
When selecting a chemical resistant pump, it is important to consider factors such as the type of chemicals being transported, the flow rate required, and the operating conditions of the pump. Different types of pumps, such as centrifugal, diaphragm, or peristaltic pumps, may be better suited for certain applications. Consulting with a pump specialist can help ensure that the right pump is selected for the job.
In conclusion, chemical resistant pumps play a crucial role in industries where corrosive chemicals are used. Their ability to withstand the damaging effects of chemicals, ensure worker safety, and provide superior performance make them an essential component of many industrial processes. By investing in quality chemical resistant pumps, companies can protect their equipment, their workers, and the environment while maintaining efficient operations.