In the world of industrial processing and mining, handling slurry—a semi-liquid mixture often consisting of fine particles mixed with water or other liquids—poses one of the most daunting challenges. The complexity and abrasive nature of slurry demand specialized equipment, with pumps playing a crucial role. Effective slurry pump solutions can enhance operational efficiency, minimize wear, and reduce maintenance costs. This article delves into the intricacies of slurry pumps, leveraging expert insights, real-world experiences, and industry-standard practices.
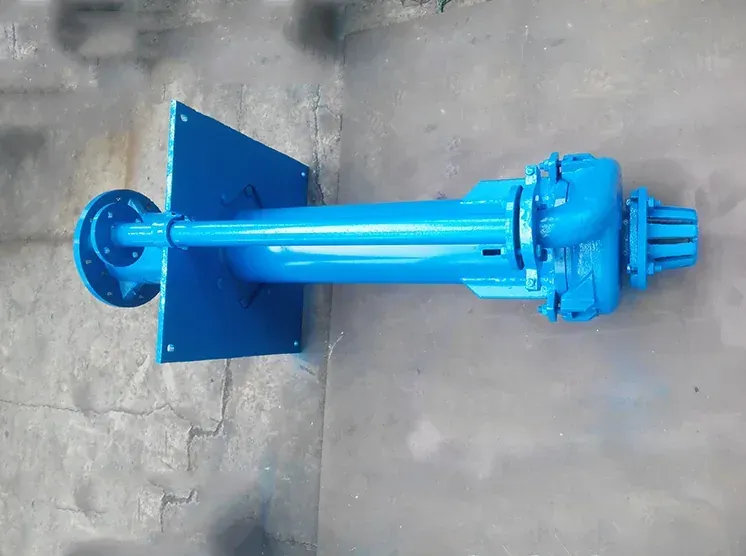
Understanding Slurry Pump Functionality
Slurry pumps are uniquely engineered to not only move but efficiently manage the flow of mixed solid and liquid materials across various industries. The design and selection of a slurry pump are dictated by the specific gravity, size, and abrasiveness of the slurry. The principal types of slurry pumps are centrifugal, positive displacement, and peristaltic pumps, each suited to different operational needs and slurry types.
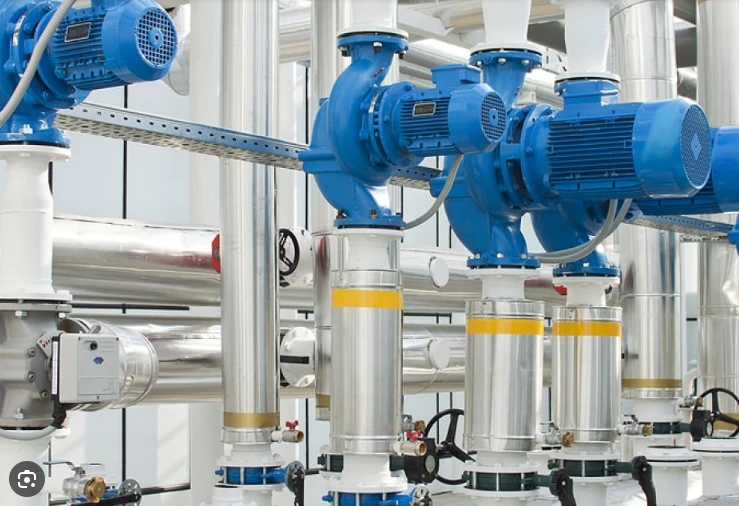
Specialized Engineering and Design
Reflecting specialized expertise, slurry pumps are constructed with robust materials that can resist wear and corrosion. Materials such as high-chrome alloys, elastomers, and ceramics are commonly employed. Centrifugal slurry pumps, known for their high-efficiency design, include hardened internal components like impellers and casings that withstand the high-impact nature of slurry.
Experience in groundwater suppression and tailing transport underscores the need for precision engineering.
The design must focus on minimizing slurry contact with sensitive parts. Reducing the impeller's speed, choosing the correct volute casing, and ensuring minimal hydraulic turbulence are critical in extending pump longevity and performance. Experts recommend a balance between cost-effective materials and durable engineering to mitigate the impact of abrasive particles in the slurry, optimizing pump life.
Real-World Applications
Industries rely heavily on slurry pumps in mineral processing, coal preparation, chemical processing, and wastewater management. For mining applications, these pumps facilitate ore extraction and transportation, emphasizing reliability under extreme conditions. Practical experiences highlight that using oversized pumps often reduces pump frequency and wear, contributing to cost savings and uninterrupted operations.
Authoritative Industry Practices
pump used for slurry
Industry leaders advocate continuous monitoring and regular maintenance as authoritative practices to maintain pump efficacy. The use of condition monitoring technologies, such as vibration analysis and thermography, aids in early detection of wear and failure points in slurry pumps, thus ensuring timely interventions and optimized performance.
The integration of Smart Pump technologies—featuring IoT and machine learning capabilities—has further revolutionized slurry pump management. This innovation enhances predictability and precision, offering data-driven insights into operational efficiencies. Operators gain improved trustworthiness in system health, enabling proactive stipulation of repair schedules reducing downtime.
Insights from Experts
Experts emphasize the importance of selecting the correct pump for specific slurry characteristics. For instance, abrasives with larger particle sizes do well with pumps that have open or semi-open impellers, reducing clogging risks. The workforce must be trained adequately to evaluate slurry viscosity and concentration aspects to ensure optimal pump performance and longevity.
Environmental and Economic Considerations
With rising environmental concerns, modern slurry pumps must align with sustainable practices. Utilizing energy-efficient models can significantly reduce both operational costs and environmental impact. Advanced systems should promote minimal fluid leakage and reduced energy consumption, aligning with global sustainability goals.
Future Innovations
The future of slurry pumping solutions lies in adaptive designs that accommodate fluctuating operational demands and environmental regulations. Continued advancements in material science and energy-efficient technologies promise enhanced resilience against the abrasive nature of slurry, combined with increased economic benefits.
In conclusion, harnessing slurry pump technology effectively requires a blend of specialized knowledge, hands-on experience, and adherence to established industry practices. As industries evolve, so too must our approaches to managing the intricate challenges presented by slurry, underscoring the importance of adopting cutting-edge technologies and sustainable practices for enhanced productivity and operational efficiency.