Designing and maintaining effective slurry pump suction piping is critical in various industrial and mining settings, where the transportation of mixed solid-liquid materials is necessary. Achieving optimal performance in slurry systems demands a thorough understanding of the intricate dynamics involved in transporting abrasive and viscous materials. A well-constructed suction piping system not only enhances pump efficiency but also extends equipment life.
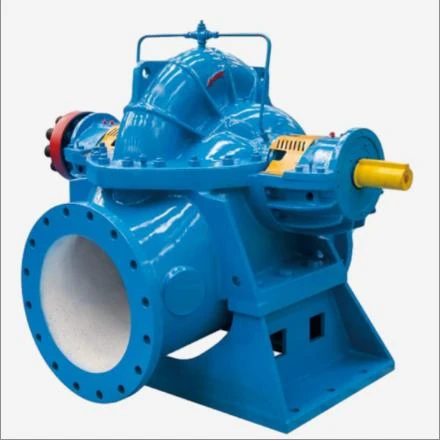
Effective suction piping begins with strategic planning and precise calculations. The selection of pipe size and material plays a pivotal role in minimizing friction and wear, thereby reducing maintenance costs over time. The diameter of the suction pipe should be large enough to handle the flow rate without causing significant friction losses. A general guideline is a ratio of the pipe diameter to particle size that prevents blockages while maintaining a steady flow rate. Moreover, materials like HDPE or steel are often preferred due to their robustness and resistance to abrasion from harsh slurry materials.
Configuration is another crucial aspect when designing suction piping. Ensuring a short, straight, and direct path for the slurry minimizes turbulence and energy loss, contributing to a more efficient pump operation. Incorporating bends or elbows should be done cautiously and minimized wherever possible; when necessary, gradual angles instead of sharp turns can dramatically decrease frictional resistance and the risk of cavitation—a phenomenon where vapor bubbles form in the liquid, causing damage and reducing efficiency.
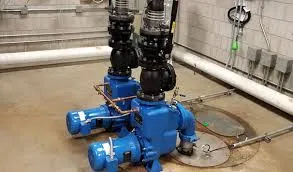
Properly calculating the Net Positive Suction Head Available (NPSHA) is imperative for preventing cavitation. The calculation ensures that the pump has adequate pressure to drive the slurry without risking cavitation problems that can prematurely wear pumps. An effective design maintains NPSHA levels above the pump's Net Positive Suction Head Required (NPSHR) by using techniques like placing the pump below the slurry source to leverage gravitational flow, effectively enhancing suction pressure.
Joint and connection integrity in the piping system cannot be understated, as leaks and loss of pressure can dramatically impact overall system efficiency. High-quality flange connections and gaskets, selected based on their compatibility with both the slurry composition and pipe material, are essential. Routine inspections and maintenance checks are fundamental, as timely detection of wear or weaknesses can prevent costly failures.
slurry pump suction piping
Maintenance procedures for slurry pump suction piping are not merely reactive but should be part of a proactive strategy. Regularly scheduled assessments focusing on wear patterns and pressure metrics help in identifying potential issues before they escalate. Implementing a comprehensive maintenance protocol, alongside detailed record-keeping of system performance and repairs, fosters a responsive approach to system management that enhances reliability and performance.
Trustworthiness in a slurry pumping system is built on consistent, reliable performance. This reliability extends from the initial design phase through to everyday operations and maintenance. By adhering to best practices and leveraging professional expertise in designing and managing slurry pump systems, operational efficiency and equipment longevity are ensured, reducing downtime and improving productivity.
The authority in slurry pump suction piping stems from a combination of practical experience and a commitment to adopting the latest technological advances. Expert engineers and operators utilize data-driven insights and field-tested techniques to refine systems continuously. Companies leading in this field offer case studies and proven outcomes, establishing themselves as thought leaders and trusted partners for businesses seeking to enhance their handling of slurries.
In conclusion, optimizing slurry pump suction piping is a multifaceted endeavor involving the careful selection of materials, strategic configuration, rigorous maintenance, and adherence to engineering principles. Industries investing in expert design and management of these systems not only achieve significant operational efficiencies but also extend the lifespan of their equipment, embodying prudence, professionalism, and expertise in their industrial operations.