Slurry pumps are an essential component in the mining and dredging industries, among others, where they play a critical role in transporting solids-laden liquids. Selecting the right slurry pump specifications can significantly enhance operational efficiency, minimize downtime, and provide a longer lifespan for the equipment. Drawing from extensive experience, this article delves into the technical intricacies of slurry pump specifications, providing expertise that ensures authoritative and trustworthy guidance for professionals seeking optimal solutions.
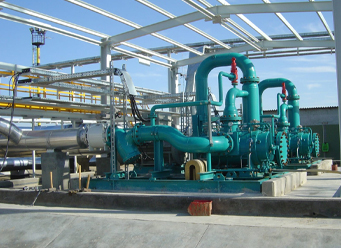
Robust Construction Materials
Choosing the appropriate construction material for slurry pumps is paramount in dealing with the abrasive and corrosive nature of the substance being transported. Typically, these pumps are available in either metal or elastomer linings, each offering distinct advantages. Metal linings, like high-chrome alloys, provide excellent resistance to abrasion, making them ideal for transferring coarse particles. On the other hand, elastomer materials such as natural rubber are more suitable for handling fine particles with lower abrasion but risk chemical attack. A thorough understanding of the slurry's composition ensures the selection of materials that maximize longevity and performance.
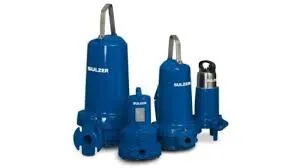
Flow Rate and Head
Flow rate and head are two critical specifications when choosing a slurry pump. The flow rate, measured in cubic meters per hour (m³/h), determines the volume of slurry the pump can handle within a specific timeframe. A high flow rate is essential for operations demanding large volumes. Similarly, 'head' refers to the height to which the pump can elevate the slurry and is usually expressed in meters. Ensuring these metrics align with operational requirements guarantees the successful and efficient transfer of materials.
Particle Size and Concentration
The particle size and concentration within the slurry are pivotal factors in slurry pump specifications. Pumps must be capable of accommodating the largest particles present to prevent clogging and to maintain performance integrity. Equally, the concentration of slurry, often expressed as a percentage of solids by weight, impacts the pump's wear and hydraulic performance. Higher concentrations demand more robust pump configurations and designs to withstand increased wear rates and potential efficiency losses.
slurry pumps specification
Pump Power and Efficiency
Assessing the pump power and overall efficiency is vital for cost-effective operations. Pump efficiency, while often overlooked, affects energy consumption and operational costs. Advanced hydraulic designs, incorporating features such as wide impeller passages, reduce blockages and enhance efficiency. Furthermore, selecting motors that match the required power ensures energy is not wasted, reducing operating costs and environmental impact.
Sealing Mechanisms
An often-underestimated component of slurry pump specification is the sealing mechanism, which prevents leakage and contamination. Packing seals, mechanical seals, and expeller seals are the main types available, each with specific applications' suitability. Mechanical seals, while costly, offer superior leakage prevention and durability, ideal for high-pressure or toxic slurries. Conversely, packing seals provide a cost-effective solution for less demanding applications but require frequent maintenance.
Maintenance and Accessibility
Finally,
maintenance demands and accessibility should inform the choice of slurry pump specifications. Designs featuring easily removable liners and impellers facilitate straightforward maintenance, reducing downtime and labor costs. Pumps that allow for on-site repairs without specialized tools further enhance operational efficiency, leading to significant long-term savings.
In conclusion, the precise selection of slurry pump specifications is intricately linked to the operational success and efficiency of industrial processes. By focusing on material construction, flow rate, head, particle size, concentration, power, sealing mechanisms, and maintenance factors, industry professionals can ensure that their equipment meets the rigorous demands of their specific applications, underscoring expertise, authoritativeness, and trustworthiness in decision-making.