Understanding and mastering the intricacies of slurry pump assembly is pivotal for industries reliant on efficient fluid management systems.
A slurry pump is an essential component designed to handle fluids containing solid particles. Its assembly process is nuanced, demanding a blend of expertise, precision, and the right tools to ensure optimal performance and durability.
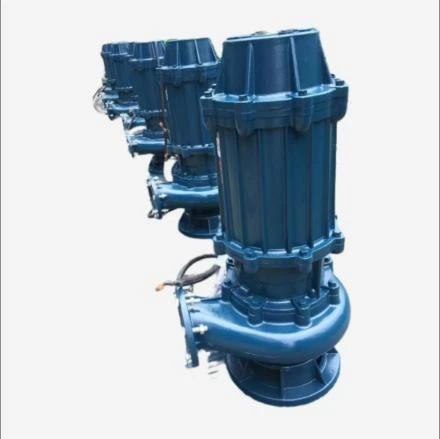
The foundation of a successful slurry pump assembly lies in understanding its anatomy and the specific requirements of the operation it will be involved in. These pumps typically consist of a casing, impellers, shaft, bearings, seals, and other auxiliary components. Each part requires meticulous handling and fitting.
When embarking on the assembly process, the initial step involves inspecting the components. It's crucial to ensure that each part is free from defects and meets the specifications required for the intended application. This includes checking the materials used in the pump’s construction, which should be selected based on the type of slurry it will handle. For instance, abrasive slurries demand wear-resistant materials to prolong the pump’s lifespan.
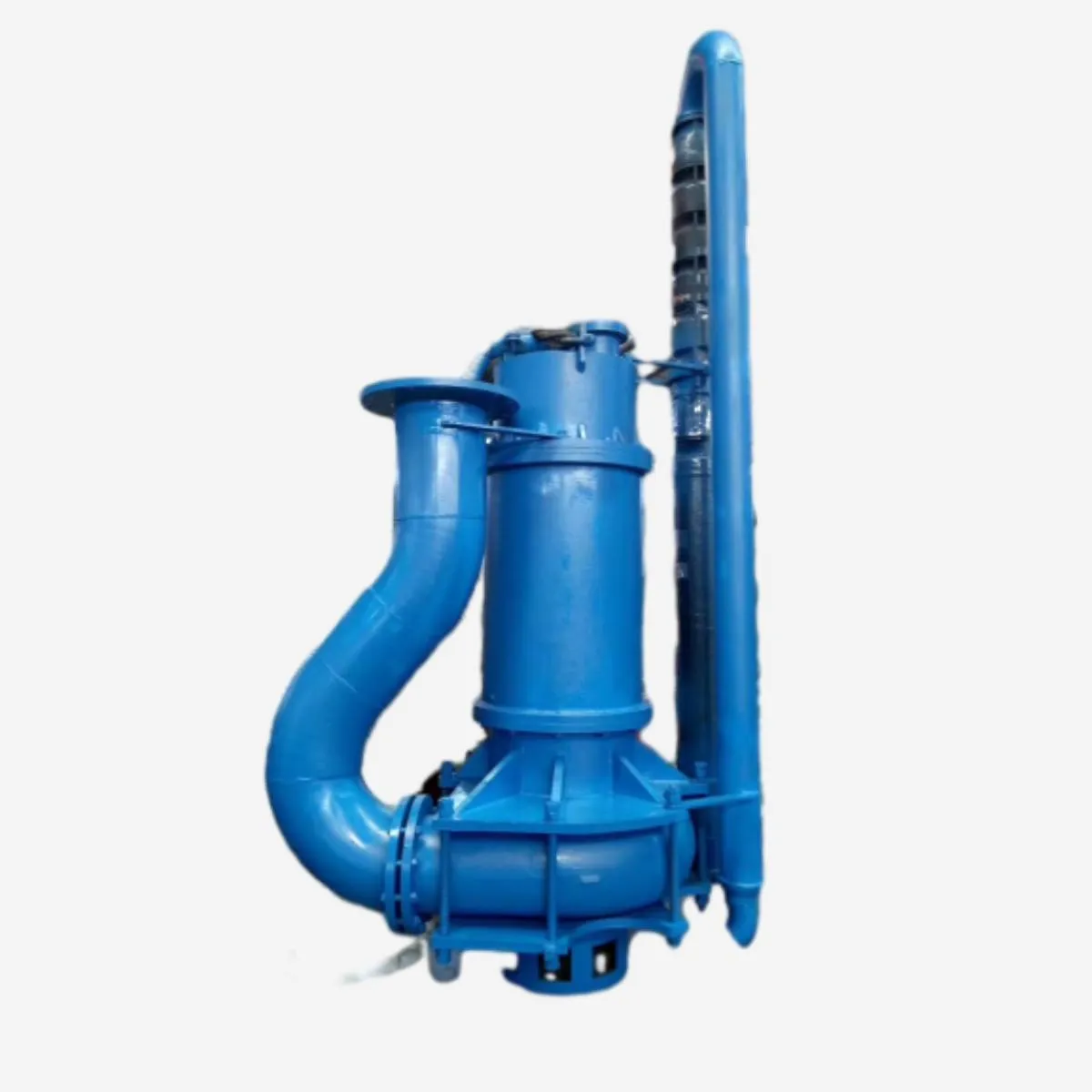
The impellers, being the heart of the pump, call for special attention. They must be fitted precisely to allow for smooth rotation and prevent premature wear. Proper alignment ensures that the impeller’s flow path is unimpeded, maximizing efficiency and minimizing the risk of energy loss.
Seals are another critical component in slurry pump assembly, playing a significant role in preventing leakage. Depending on the pump design, mechanical seals or gland packing may be used. Mechanical seals are preferred in many applications due to their longevity and reliability. The selection and installation of seals require a deep understanding of the operating environment the pump will be exposed to, such as pressure levels, fluid temperature, and particulates present.
Bearings support the shaft and allow for smooth operation. Selecting the right type and size of bearings is essential, as they must withstand the operational loads and stresses without succumbing to failure. Proper lubrication during installation is equally important to mitigate friction and wear.
slurry pump assembly
Assembly experts stress the importance of adhering to the manufacturer’s guidelines during the installation process. Deviations from these guidelines can lead to improper fitment, resulting in reduced efficiency or mechanical failures. Furthermore, employing precision instruments for measuring and aligning components is a critical practice that enhances accuracy and alignment during assembly.
Once the assembly is complete, it’s imperative to conduct rigorous testing to verify the integrity and functionality of the pump. This typically includes operational tests under simulated conditions that replicate real-world scenarios. Parameters such as flow rate, pressure, and temperature are monitored to ensure the pump operates within the designed specifications.
Proper documentation during the assembly and testing phase is essential to maintain a record of compliance with industry standards. This documentation provides traceability and accountability, reinforcing the pump's reliability and the assembler's expertise.
For those involved in assembly, continuous learning and staying updated with the latest industry advancements and innovations is vital. This not only augments one’s expertise but also aligns the assembly practices with cutting-edge developments and technologies.
In conclusion, a meticulous and informed approach to slurry pump assembly not only enhances the pump's performance but also elevates the reliability and efficiency of the entire fluid handling system. For industries, this translates into reduced downtime, lower maintenance costs, and improved productivity. Investing in knowledgeable and skilled personnel for the assembly process is therefore a strategic move that reaps long-term benefits. By emphasizing expertise, accuracy, and stringent adherence to best practices, the challenges of slurry pump assembly can be effectively navigated, ensuring that the systems remain robust and efficient in the most demanding applications.