Pumping slurries presents unique challenges, demanding a specialized approach to ensure efficiency and longevity of pumping equipment. The key to successfully managing slurry pumping lies in a deep understanding of the material properties and the technology required to handle them effectively. This expertise allows for greater adaptability in industrial processes, be it mining, dredging, or wastewater treatment.
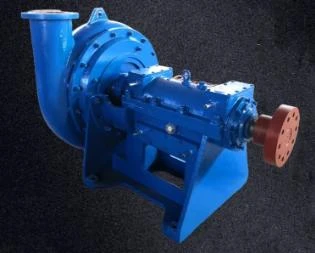
Slurries are mixtures of solids and liquids, typically with a significant concentration of abrasive particles. These materials can cause severe wear and tear on pumps, leading to increased maintenance costs and downtime. Therefore, choosing the right pump is crucial. Centrifugal pumps are commonly used for slurry applications due to their ability to handle high volumes of liquids and basic granular solid materials. However, they require specific design modifications, such as larger impellers and wear-resistant components, to cater to the abrasive nature of slurries.
Expert experience reveals that material selection for pump components is a foundational aspect of handling slurries. High-chromium iron, carbide-based materials, and elastomers like rubber and polyurethane are generally recommended, owing to their resistance to abrasion and corrosion. Engineers often prefer hard facing welded layers of specific materials to reinforce components such as the impeller, casings, and even the shafts. This allows for maximized wear life and reduced costs over time, aligning with long-term operational goals.
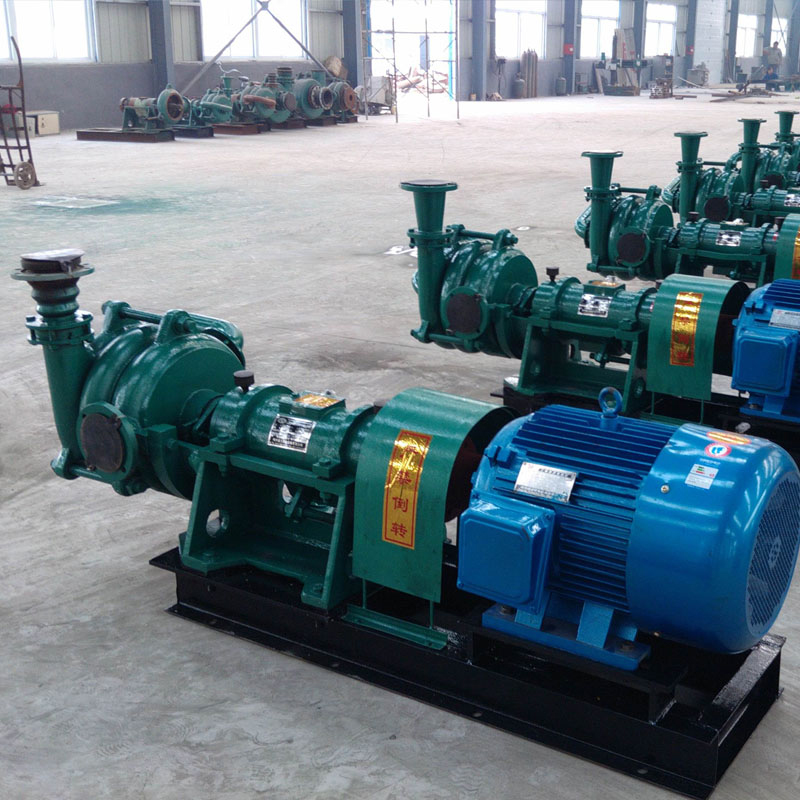
In maintaining authority in the domain of slurry pumps, consider advancements in pump technology focusing on efficiency improvements. Variable speed drives (VSDs) enable pumps to operate with precise control, adapting swiftly to changing slurry consistency and process demands. Modern monitoring systems also provide real-time data analytics, allowing for proactive maintenance rather than reactive repairs. This innovative approach reduces unexpected failures, enhancing trust in the deployment of slurry pumps within critical operations.
pumping slurries
Trustworthiness in slurry pumping operations can be bolstered by meticulous design considerations. Ensuring the appropriate pump size and type not only prevents overloading but also extends the operational lifespan.
An industry best practice involves conducting detailed preliminary tests. Simulations that model the slurry's behavior within the pump can predict potential points of failure and opportunities for efficiency enhancements. By employing computer-aided design software and computational fluid dynamics, engineers can optimize pump performance significantly before actual deployment.
Furthermore, the expertise extends beyond pump design and material selection to encompass system layout. Ensuring that the piping network is designed to minimize curves and sharp angles can reduce the wear rate by limiting turbulence. This, along with careful calculation of head and flow rate requirements, ensures that the pump operates within its designed specifications, thereby ensuring longevity and reliability.
Achieving high reliability and efficiency also requires well-structured maintenance routines. Regular inspection and scheduled replacement of worn components can prevent long-term damage. Employing condition-monitoring technologies, such as vibration analysis and thermal imaging, can give early warnings of potential issues, thereby safeguarding against unexpected breakdowns.
In conclusion, pumping slurries effectively involves a multi-faceted approach centered around experience, expertise, authoritativeness, and trustworthiness. By aligning pump selection with material properties and leveraging modern technology for precise control and predictive maintenance, industries can optimize their operations. The integration of careful design, innovative materials, and proactive system management encompasses the hallmarks of excellence in slurry pumping, ensuring that operations remain smooth, cost-effective, and reliable.