High pressure slurry pumps are integral components in a variety of industrial sectors, renowned for their robustness and efficiency in moving viscous, abrasive, and corrosive fluids. As industries continue to rely on these powerful machines for critical operations, understanding the key factors that contribute to an optimal slurry pump setup becomes imperative.
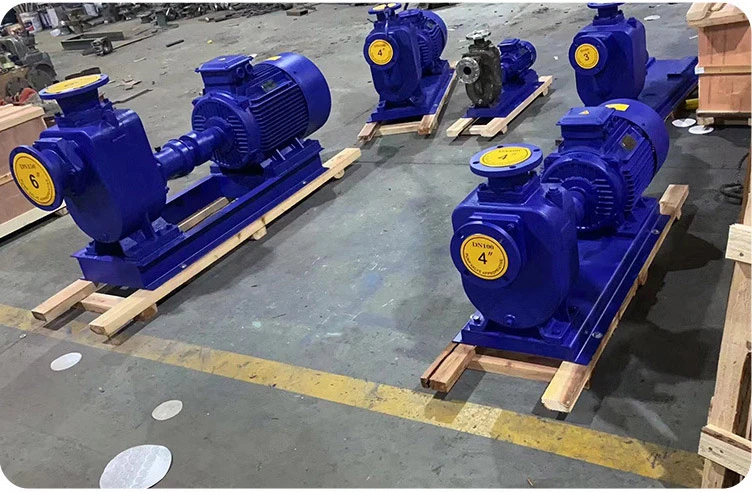
When selecting a high pressure slurry pump, the first consideration should be the pump's material construction. Pumps constructed from hard alloys or elastomers are often preferred due to their ability to withstand the corrosive nature of slurries, which can vary significantly in terms of their physical properties and chemical composition. Ensuring that the pump material aligns with the slurry’s nature can greatly enhance its lifespan and operational efficiency.
One cannot overlook the importance of the pump's design, which directly impacts its efficiency and longevity.
High pressure slurry pumps should feature advanced hydraulic designs that emphasize reduced turbulence and friction. By optimizing the impeller and casing designs, industries can achieve higher efficiency rates which translate into energy savings and lower operating costs over time. Furthermore, a well-designed pump minimizes downtime, a critical factor in industries such as mining and construction where continuous operations are pivotal to profitability.

For those operations demanding high reliability and minimal maintenance, selecting a pump with a proven mechanical seal system is crucial. Mechanical seals prevent slurry from leaking into the mechanical parts of the pump, thereby preventing potential failures. Pumps with innovative seal planning allow for easy access and repair, enhancing their trustworthiness and ensuring less downtime. Implementing condition monitoring systems can further help in predictive maintenance, ensuring longevity and consistent performance.
high pressure slurry pump
In addition to individual pump specifications, integrating the pump into a broader system requires careful consideration of flow dynamics. Ensuring that the pump complements the operational environment necessitates a comprehensive understanding of the system’s demands, ensuring a seamless integration that maximizes performance while minimizing energy consumption. Studies have shown that optimal pump-system matching can significantly boost productivity and enhance return on investment.
Field experience shows that the choice of manufacturer plays an influential role in determining the slurry pump’s overall reliability. Opting for established manufacturers known for their expertise in slurry systems offers peace of mind and a wealth of industry experience. These manufacturers typically provide comprehensive support, including customization options, expert consultation, and after-sales services that bolster trust in their products.
Finally, industrial players must also adhere to strict environmental and safety regulations, ensuring that high pressure slurry pumps not only perform well but do so sustainably. Choosing pumps with energy-efficient motors and utilizing environmentally friendly materials and lubricants demonstrates a commitment to sustainable practices. This aligns with evolving industry standards and enhances the operation's overall trustworthiness.
In conclusion, a strategic approach to selecting and utilizing high pressure slurry pumps—focusing on material choice, design excellence, mechanical reliability, system integration, manufacturer reputation, and sustainability—will ensure that industrial operations operate efficiently, safely, and cost-effectively. This level of diligence not only satisfies immediate operational demands but also aligns with long-term business objectives and regulatory requirements, cementing a reputation of reliability and expertise in the market.