Flue gas desulfurization (FGD) pumps play a crucial role in industrial processes, particularly in power plants, where they are used to remove sulfur dioxide (SO2) from exhaust gases. With increasing environmental regulations, the efficiency and reliability of these pumps have gained paramount importance. This article aims to delve deep into the intricacies of FGD pumps, focusing on their application, operation, and the factors that determine their efficacy.
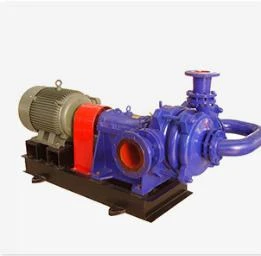
Flue gas desulfurization pumps are engineered to handle the abrasive and corrosive slurry resulting from the FGD process. This process generally involves a reaction between the flue gases and a sorbent, like limestone, resulting in the production of gypsum. The pump's primary responsibility is to transport this high-density gypsum slurry safely and efficiently, minimizing downtime and maintenance.
The experience of using FGD pumps highlights the importance of selecting the right material and design. Pumps constructed from high-alloy stainless steels or lined with rubber or other corrosion-resistant materials are preferred to mitigate the corrosive effects of the slurry. This material selection is critical for extending the pump's lifespan and reducing the frequency of costly repairs.
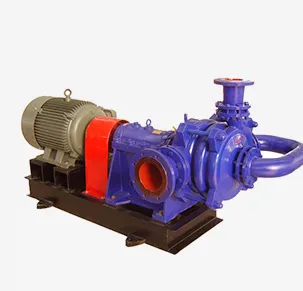
Expertise in the setup and operation of these pumps cannot be overstated. Proper installation and alignment are critical to avoid vibrations, which can lead to premature wear and tear. Moreover, understanding the dynamics of slurry flow, such as the concentration of solids, particle size, and velocity, is vital for optimizing pump performance. It's advisable for operators to collaborate closely with the pump manufacturers to ensure the configuration is tailored to their specific operational needs.
flue gas desulfurization pump
When it comes to FGD pumps' authoritativeness, industry standards and certifications play a substantial role. Pumps that comply with ISO 9001 or ASME standards offer added assurance regarding their quality and reliability. Additionally, manufacturers with extensive research and development programs and those who offer comprehensive after-sales support are often more authoritative in the industry. Their in-depth knowledge and commitment to innovation ensure that their pumps meet the ever-evolving demands of environmental protection.
Trustworthiness in FGD pumps is built through demonstrated reliability and performance over time. Regular monitoring and maintenance are critical components of a trust-based operating strategy. Implementing a preventative maintenance schedule ensures that issues are detected and resolved before leading to significant failures. Furthermore, integrating modern technologies, such as IoT sensors and real-time data analytics, can provide actionable insights into the pump's performance, leading to more informed decision-making.
In conclusion, flue gas desulfurization pumps are indispensable in the arsenal of solutions for reducing atmospheric pollutants. Their importance demands a focus on selecting the appropriate materials, expertise in handling the pumps, adherence to established standards, and a structured maintenance approach. As environmental regulations continue to tighten globally, the role of FGD pumps will only grow more significant, underscoring the need for continued innovation, stringent quality controls, and robust operator education. This comprehensive focus ensures these systems contribute effectively to cleaner industrial operations and a healthier environment.