In the realm of industrial processes, double suction pumps hold a critical position due to their efficiency and reliability. Designed to accommodate high flow rates while maintaining low operating speeds, these pumps are indispensable in various sectors including water treatment, oil refining, and power generation. Understanding the anatomy and operational principles of a double suction pump is key for professionals aiming to enhance system performance and reliability. This article delves into the comprehensive details of double suction pump diagrams, reflecting on expert knowledge and real-world experiences to illuminate their application and operation.
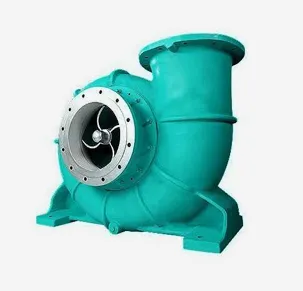
A double suction pump operates on the principle of axial symmetry, which significantly reduces axial load. What sets double suction pumps apart from their single suction counterparts is the incorporation of dual impellers that draw fluid from both sides. This design feature not only stabilizes the axial force but also allows for a more balanced flow. By effectively mitigating vibrations, these pumps ensure a longer service life and reliable performance, making them highly preferred for heavy-duty applications.
The core components of a double suction pump include the casing, impellers, bearings, shaft, and sealing systems, each meticulously designed to serve a specific function. The casing, often split horizontally, facilitates easy maintenance and inspection without dismantling the entire pump. It houses the impellers and assists in directing the flow of fluid towards them. Made from robust materials like cast iron or stainless steel, the casing is engineered to withstand the rigors of high-pressure environments.
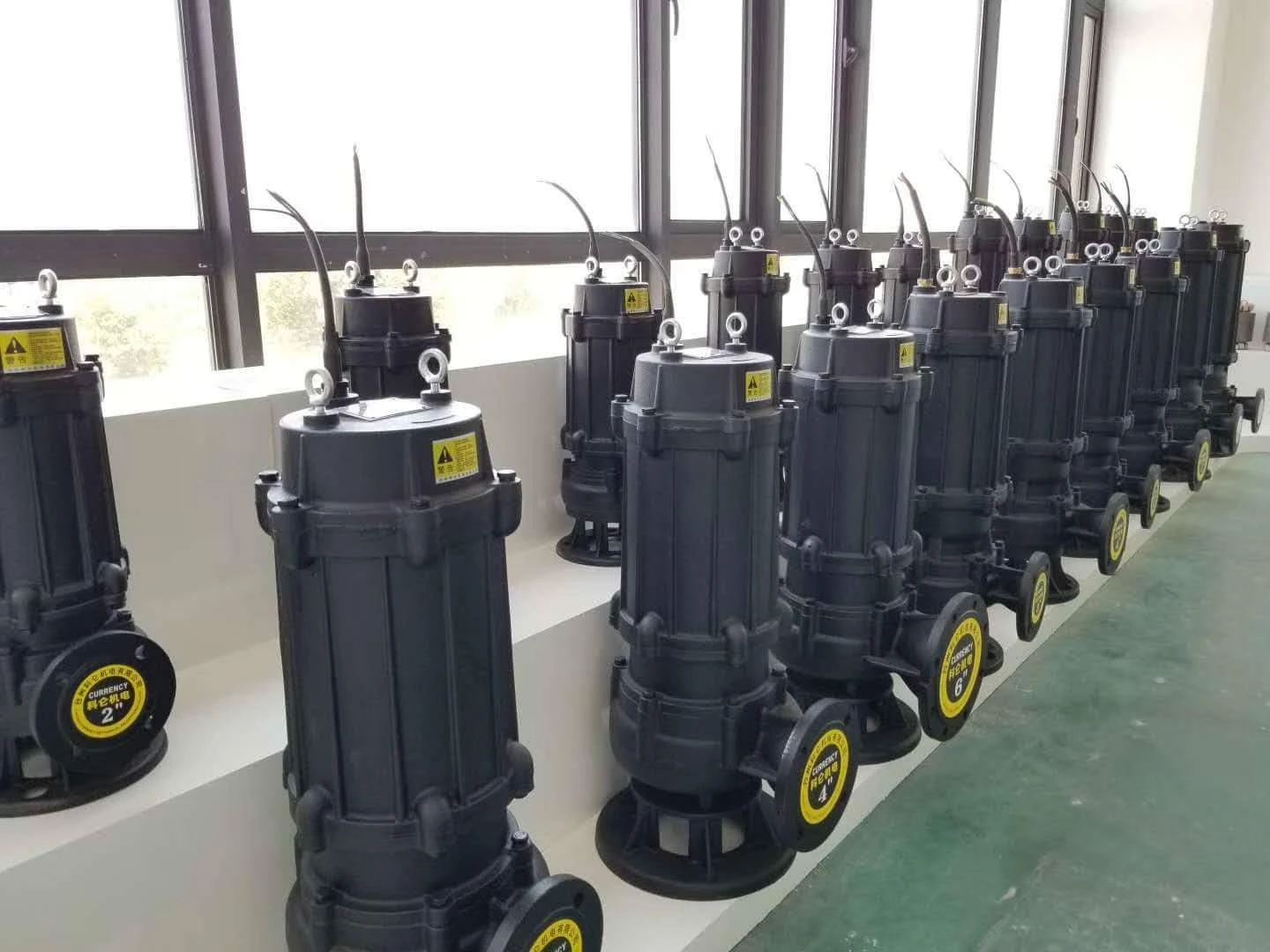
Impellers are the heart of the double suction pump system. Crafted to precision, they are responsible for imparting velocity to the fluid. In a double suction design, the impeller draws fluid from both sides, doubling the intake area compared to a single suction pump. This unique arrangement minimizes the net positive suction head required, simultaneously enhancing hydraulic performance and reducing the risk of cavitation.
Bearings play a pivotal role in supporting the rotor and absorbing radial and axial loads. The optimal selection and maintenance of bearings are crucial for minimizing friction and wear, thus ensuring smooth operation. Bearings in high-performance double suction pumps are often equipped with sophisticated lubrication systems to extend their lifespan and improve efficiency.
The shaft interconnects the mechanical components, transmitting torque from the motor to the impellers. Precision in shaft alignment is vital, as misalignment can lead to premature wear and catastrophic failures. High-quality materials, such as stainless steel alloys, are commonly used for shafts to resist corrosion and fatigue under operational stress.
double suction pump diagram
Sealing systems are essential for preserving the internal environment of the pump, preventing leakage, and ensuring operational safety. Double suction pumps typically employ mechanical seals or packing seals to maintain robustness in their performance. Each type of seal has its applications, with mechanical seals offering superior leakage control and durability in demanding conditions.
Real-world application of double suction pumps requires understanding the specific field conditions and operational stresses. For instance, in water utilities, the optimized hydraulic design translates into significant energy savings and reduced lifecycle costs. In contrast, the oil industry values the reliability and low maintenance demands due to the pumps' ability to handle corrosive and abrasive fluids.
Additionally, expertise in the installation process is crucial to leverage the full potential of double suction pumps. Proper alignment through laser tools, secure foundation mounting, and precise adjustments ensure that the pumps perform optimally. Regular monitoring and diagnostic procedures, such as vibration analysis and thermal imaging, are recommended to detect anomalies and preempt failures.
Establishing authoritativeness involves affiliating with credible institutions and adhering to industry standards like ISO and ASME for pump manufacturing and testing. Compliance with these standards ensures that the pump designs meet rigorous quality and performance benchmarks.
In conclusion, double suction pumps represent a synergy of advanced engineering and practical application. Their intricate design and operational efficiency are a testament to their enduring value in industrial systems. As professionals continue to explore innovative ways to enhance pump performance, the insights drawn from real-world experiences and expert knowledge ensure these robust machines remain integral to fluid management systems worldwide. By focusing on thorough maintenance practices and adopting advanced monitoring technologies, stakeholders can significantly enhance the trustworthiness and longevity of double suction pumps, fostering continued success across diverse industries.