Slurry pumps are indispensable in industries like mining, metallurgy, and chemical processing, where handling abrasive and corrosive materials is routine. To ensure optimal performance and longevity of these pumps, understanding the various slurry pump parts and their roles is crucial for both operators and businesses. As a seasoned professional with extensive experience in pump maintenance and optimization, I will delve into the intricate details of slurry pump components, drawing on expertise and authoritative insights to guide you through this essential topic.
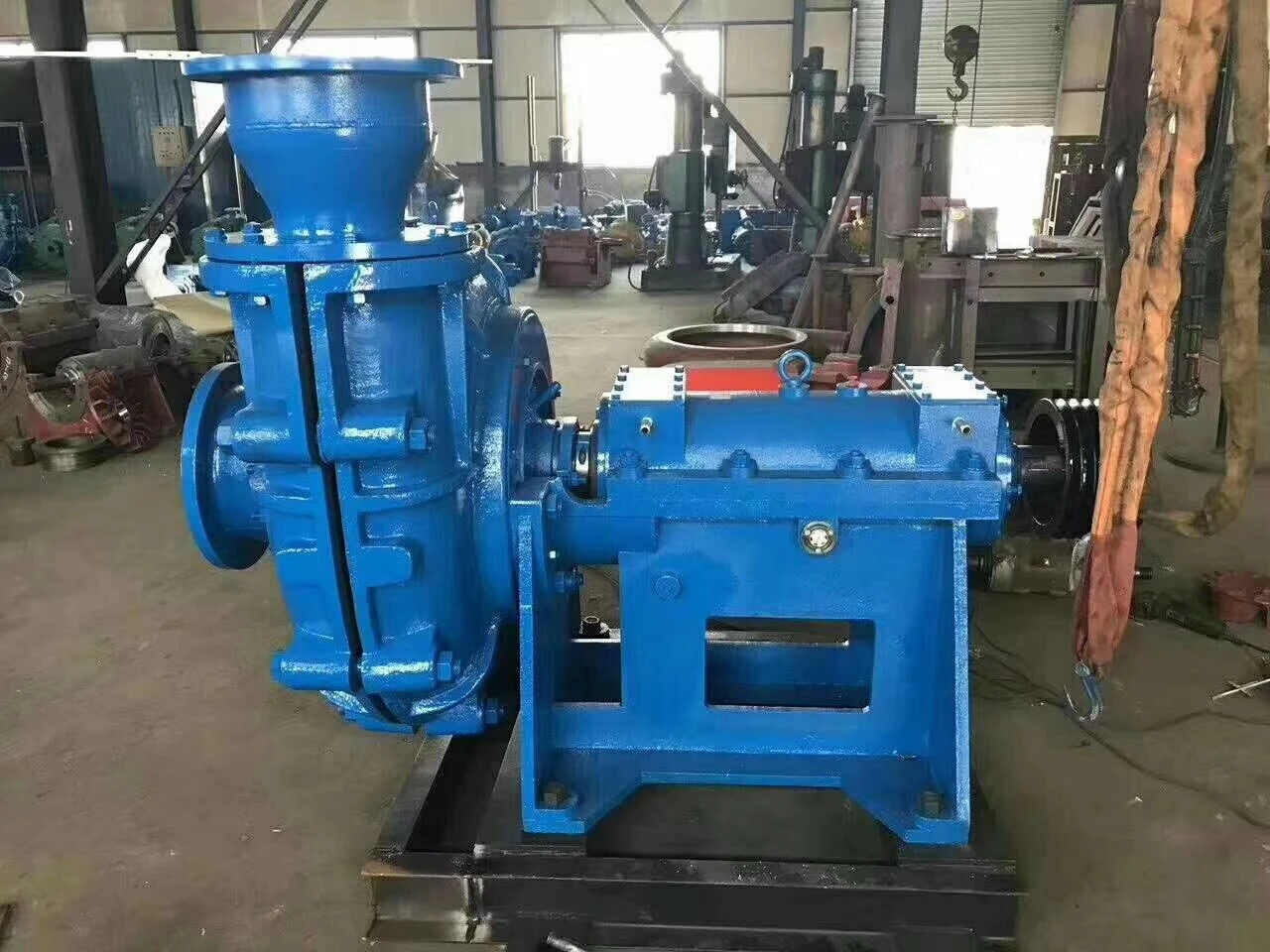
The heart of every slurry pump lies in its impeller, which is the rotating component responsible for adding velocity to the slurry. Impellers come in different types — open, closed, and semi-open — each designed for specific slurry types and concentrations. Open impellers, for example, are more suited for handling large solids, due to their non-clogging properties. Choosing the right impeller type is critical, as it directly impacts the pump's efficiency and wear rate.
The pump casing, another vital component, provides the structural integrity needed to withstand high pressures and abrasive wear. Casings are typically constructed from high-chrome alloys or elastomers, materials known for their durability and resistance to corrosion and abrasion. Selecting the appropriate material for the casing is paramount, as it helps reduce maintenance costs and downtime attributed to wear.
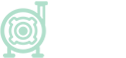
Aside from impellers and casings, slurry pumps contain shaft seals, which prevent leakage of the slurry and are essential for maintaining operational safety and efficiency. There are several seal options, including gland packing, expeller seals, and mechanical seals. Each has its advantages and considerations. For instance, gland packing is widely used for its cost-effectiveness but may require regular adjustments and maintenance. Mechanical seals, on the other hand, offer superior leak prevention but at a higher initial cost.
slurry pump parts
Moreover, the bearings are crucial for the pump's smooth operation, ensuring the shaft and impeller rotate without interference. Proper lubrication and maintenance of bearings are imperative to prevent premature failure and enhance the pump's lifespan. Recognizing early signs of bearing wear, such as unusual noise or vibration, can significantly mitigate potential issues.
Wear plates and liners are often overlooked but play a crucial role in protecting the pump's internal components from abrasion. Regular inspection and timely replacement of these parts are recommended, particularly in heavy-duty applications where the wear rate is notably higher. Utilizing high-grade materials such as tungsten carbide for these components can extend their service life.
Reliability in slurry pump operation is integral to maintaining productivity. Therefore, understanding and selecting the appropriate pump parts, coupled with regular maintenance, can greatly enhance operational efficiency. When procuring slurry pump parts, it is advisable to work with reputable suppliers who offer parts manufactured to international standards, ensuring quality and compatibility with your existing systems.
In conclusion, slurry pump parts are critical to the durability and performance of pumps in abrasive environments. A thorough understanding of these components, supported by professional expertise, not only ensures operational efficiency but also builds trust and credibility in an industry where reliability is paramount. By focusing on expert advice and adhering to best maintenance practices, businesses can optimize their slurry pump systems for long-term success.