Navigating the landscape of centrifugal chemical process pumps can be a transformative experience for industries reliant on efficient fluid handling. These pumps, essential in numerous sectors—ranging from pharmaceuticals to petrochemicals—embody specialized engineering, enabling them to withstand the rigors imposed by chemically aggressive and physically demanding environments. Their selection, integration, and maintenance represent crucial decisions impacting operational efficacy and safety. Drawing from a wealth of expertise, this guide will illuminate the key aspects of centrifugal chemical process pumps, underpinned by real-world insights and authoritative recommendations.
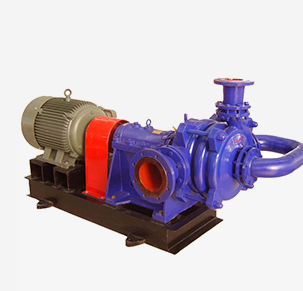
Centrifugal chemical process pumps serve as the backbone for fluid movement in industrial applications. Unlike their generic counterparts, these pumps are designed with materials and features suited to withstand corrosive and abrasive substances. Common materials include stainless steel, Hastelloy, and other corrosion-resistant alloys. The inherent versatility of centrifugal pumps facilitates handling varying viscosities and densities, a necessity in chemical processing where fluid properties can fluctuate.
A pivotal consideration in choosing the right pump revolves around material compatibility. Ensuring that the pump's components can withstand the chemicals they will contact is paramount. Failures due to corrosion or material degradation can lead to costly downtimes and hazardous situations. Thus, leveraging expertise in chemical compatibility, often offered by manufacturers and consultants, can significantly alleviate these risks, enhancing operational trustworthiness.
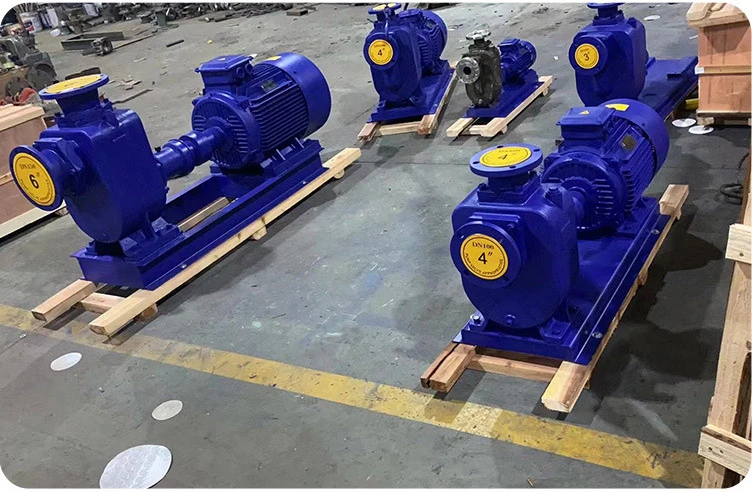
Incorporating advanced technologies has propelled the efficiency and reliability of centrifugal chemical process pumps. Innovations like seal-less pump designs and magnetically driven pumps minimize the risk of leaks—an essential feature when dealing with harmful substances. The implementation of variable frequency drives (VFDs) allows precise control over pump operations, optimizing energy consumption and reducing wear and tear. Real experience underscores the value of choosing pumps with these capabilities, as they not only improve process efficiency but also extend the life of the equipment.
Authoritative industry standards, such as those from the American National Standards Institute (ANSI) and the International Organization for Standardization (ISO), provide a solid framework for the design and safety of these pumps. Compliance with these standards ensures that pumps meet necessary safety and performance benchmarks, which is critical for maintaining an authoritative stance in safety and quality assurance. It is advisable to select pumps that not only adhere to these standards but exceed them, establishing a margin of safety and reliability.
centrifugal chemical process pumps
Regular maintenance and monitoring form the bedrock of maximizing the lifespan and performance of centrifugal chemical process pumps. Real-world applications demonstrate that proactive maintenance strategies—such as regular inspections, condition monitoring, and predictive maintenance—can mitigate unscheduled downtimes. These strategies allow operators to identify potential issues before they escalate, maintaining an environment of trust and reliability in process integrity.
Expertise in pump operation also involves understanding the nuances of system integration. Critical factors include the correct sizing and matching of pumps to system requirements, ensuring that pump curves align with the system’s operation points. Inappropriate sizing can lead to operational inefficiencies, including cavitation and increased wear. Consultations with pump specialists can provide insights into optimal system design, safeguarding against these inefficiencies.
In the diverse applications of centrifugal chemical process pumps, industry experience consistently highlights the importance of adaptability and customization. Different processes demand different setups; hence, pumps are often customized to suit particular operational and environmental conditions. Manufacturers frequently offer tailored solutions that align with unique process requirements, ensuring efficiency and compliance with industry-specific regulations.
In conclusion, understanding and deploying centrifugal chemical process pumps demands a composite of real-world experience, technical expertise, and adherence to industry standards. By focusing on material compatibility, advanced technology integration, compliance with authoritative standards, and proactive maintenance strategies, industries can significantly enhance their operational effectiveness. These pumps, while sophisticated, are accessible to those who approach their deployment with informed strategy and calculated diligence. By prioritizing these tenets, industries can navigate the complexities of chemical processing with confidence and authority, ensuring reliability and trust in their fluid handling operations.