In the world of fluid handling, especially when it comes to peristaltic pumps, a critical component that ensures efficacy and safety is the tubing used. Chemical resistant tubing for peristaltic pumps is at the intersection of innovation and necessity, and plays a pivotal role in numerous industries ranging from pharmaceuticals to food and beverage production. Not all tubing is created equal when it comes to chemical resistance, and selecting the right tubing is not merely a matter of durability but an assurance of process integrity and operator safety.
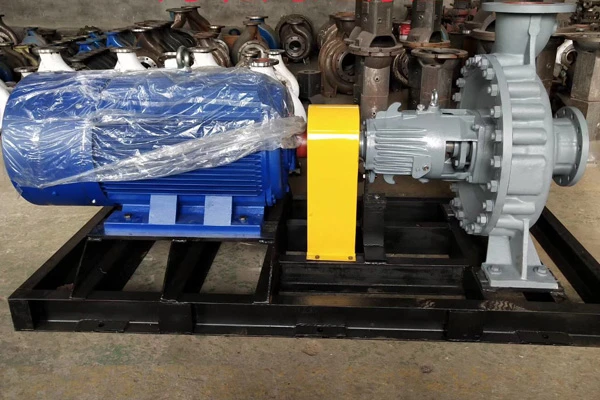
Peristaltic pumps operate on a simple but highly effective principle liquid or fluid is transported through a flexible tube that gets compressed and released in a rotational manner. The tubing's flexibility is what facilitates the pump's function, but it's the chemical resistance of the tubing material that defines the range of fluids it can handle.
Several materials are employed in the manufacture of chemical resistant tubing, including, but not limited to, silicone, thermoplastic elastomers, and fluoropolymers like PTFE (Polytetrafluoroethylene). Each of these materials has distinct properties.
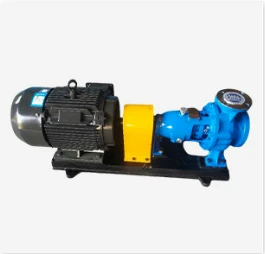
Silicone tubing is highly flexible and easy to handle, making it a preferred choice in applications where cleanability and biocompatibility are prioritized. However, it’s not suitable for aggressive chemical environments. Thermoplastic elastomers can combine flexibility with varying degrees of chemical resistance, offering a middle ground. On the other hand, fluoropolymer tubing, which includes PTFE, stands out for its superior chemical resistance, and withstands harsh solvents, acids, and bases. This makes fluoropolymer tubing a viable option for demanding applications.
The expertise required in selecting the right tubing for a peristaltic pump is paramount. It requires a deep understanding of the fluid characteristics and the operating conditions of the system. Factors such as temperature, pressure, and the specific chemical composition of the fluid need careful consideration. For instance, PTFE might be the best choice for its chemical inertness, but if the situation requires continuous flexing at lower temperatures, specialized thermoplastic elastomers or alternate versions of fluoropolymer might be more effective.
Selecting the correct chemical resistant tubing also impacts the maintenance cycles and the overall lifespan of the equipment. Incorrect selection can lead to frequent tubing failures, potential safety risks, and costly downtime. Specialists in fluid management systems underscore the importance of compatibility testing — this ensures the selected tubing material can withstand the planned applications. Often, the material experts and applications engineers collaborate to benchmark and suggest optimizations, testing the tubings under simulated conditions before final rollouts.
chemical resistant tubing for peristaltic pump
In terms of authoritativeness, the guidance from industry standards and certifications can’t be overstated. Chemical resistant tubing should adhere to standards such as ISO, FDA, and USP Class VI, as these assure quality and safety benchmarks are met. Suppliers with extensive experience in the industry often offer more reliable products, as they bring years of research and development into material enhancements.
Trust is a keyword in this domain, as stakeholders rely on product claims certified through rigorous testing and validation. When sourcing tubing, partnership with well-reputed manufacturers known for transparency in test results, adherence to international standards, and responsive technical support is indispensable.
Moreover, process owners should remain informed of technological advancements. Innovations like multi-layer tubing technology enable combining various materials to leverage their collective strengths, thus introducing new possibilities in chemical handling. Such developments are crucial in expanding the efficiency envelope of peristaltic pumps.
Summary experiences from industry veterans reveal not just lessons in material selection but highlight loyalties formed over specific brands known for robust performance in challenging applications. These collective testimonials build an intrinsic trust towards certain products and suppliers.
Conclusively, excellence in chemical handling with peristaltic pumps hinges largely on the integrity of chemical resistant tubing. With the ever-increasing diversity of chemical formulations across sectors, staying informed through authoritative sources and embracing technological advancements can yield superior process outcomes, preventing unnecessary complications and opening the way to innovative fluid handling solutions.