Slurry pumping is a critical aspect of many industries, including mining, construction, and wastewater treatment. It involves the transportation of a mixture of water and solid particles, known as slurry, through a system of pipes using pumps.
The first step in slurry pumping is selecting the appropriate pump for the job. There are several types of pumps that can be used for slurry pumping, including centrifugal pumps, diaphragm pumps, and piston pumps. The choice of pump depends on factors such as the size and concentration of the solid particles in the slurry, as well as the distance and elevation that the slurry needs to be pumped.
Once the right pump is selected, it is important to properly install and maintain the pump to ensure efficient and reliable operation. This includes ensuring that the pump is correctly aligned, that the seals are in good condition, and that the pump is operated within its specified operating parameters.
One of the key challenges in slurry pumping is managing the abrasive nature of the slurry. The solid particles in the slurry can cause wear and tear on the pump components, leading to increased maintenance and downtime. To combat this, pumps used for slurry pumping are often equipped with wear-resistant materials and coatings, and regular maintenance schedules are put in place to monitor and replace worn parts To combat this, pumps used for slurry pumping are often equipped with wear-resistant materials and coatings, and regular maintenance schedules are put in place to monitor and replace worn parts
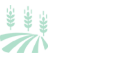
To combat this, pumps used for slurry pumping are often equipped with wear-resistant materials and coatings, and regular maintenance schedules are put in place to monitor and replace worn parts To combat this, pumps used for slurry pumping are often equipped with wear-resistant materials and coatings, and regular maintenance schedules are put in place to monitor and replace worn parts
slurry pumping.
Another challenge in slurry pumping is dealing with the high viscosity of the slurry. High viscosity can make it difficult for the slurry to flow smoothly through the pump and pipes, leading to blockages and reduced efficiency. To address this, pumps used for slurry pumping are designed to handle high viscosity fluids and are often equipped with features such as larger clearances and specialized impellers to improve flow.
In addition to selecting the right pump and managing wear and viscosity, it is important to also consider the environmental impact of slurry pumping. Slurries often contain hazardous materials that can pose a risk to the environment if not properly managed. It is crucial to follow proper containment and disposal procedures to prevent contamination of waterways and soil.
Overall, slurry pumping plays a vital role in many industries by efficiently moving material from one location to another. By understanding the challenges and best practices associated with slurry pumping, operators can ensure smooth and reliable operation of their pumping systems while minimizing environmental impact.