The Large Industrial Sludge Slurry Pump Mining Wear-resistant (Large Industrial Sludge Slurry Pump Mining Wear-resistant) stands at the forefront of the industrial pump market, setting benchmarks in durability, efficiency, and adaptability for harsh mining and heavy-duty slurry applications. In the rapidly evolving domain of global mineral processing and sludge management, high-performance wear-resistant slurry pumps have become indispensable for ensuring operational continuity and reduced lifecycle costs.
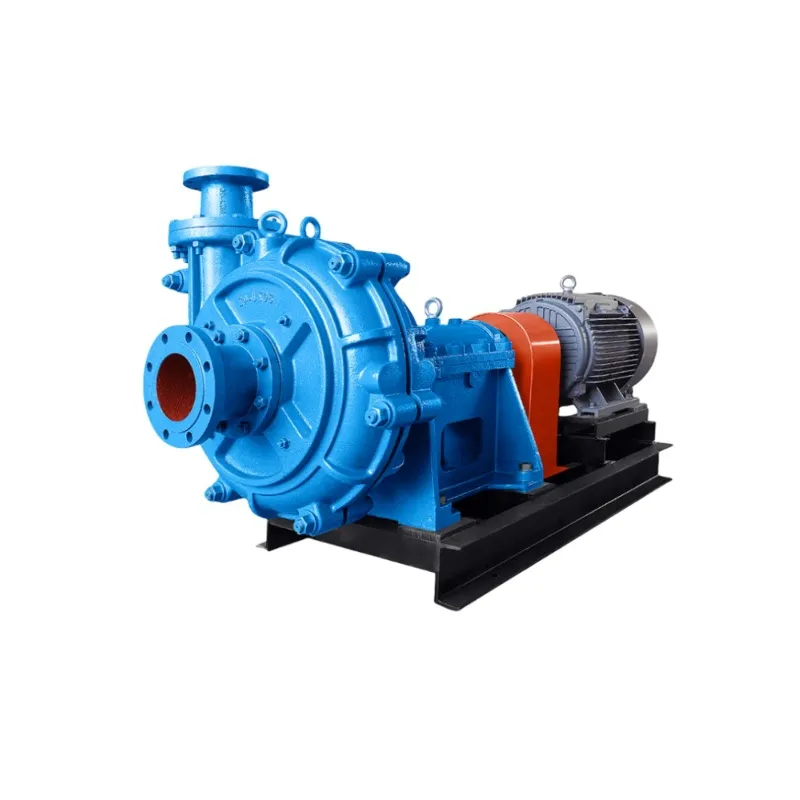
1. Industry Trends & Market Data: The Demand for Wear-Resistant Slurry Pumps
- Global Market Size: The worldwide demand for industrial sludge and slurry pumps reached $2.60 billion in 2023 and is forecasted to grow at a CAGR of 5.2% through 2028 (Grand View Research).
- Mining Sector Usage: Over 44% of all large centrifugal slurry pumps are deployed in mining and mineral processing applications (Minerals Engineering, 2023).
- Wear-Resistance Focus: 68% of purchasing managers rank wear life and total cost of ownership ahead of initial pump price (Mining Magazine Survey, 2023).
- Cross-Industry Adoption: Sectors such as petroleum, steel, electric power, and chemical processing have reported a 18% YOY increase in deploying heavy-duty slurry pumps (Global Industrial Slurry Trends, 2023).
2. Technical Parameters and Product Specifications
Key Technical Parameters
Model | Flow Rate (m³/h) | Head (m) | Power (kW) | Max Particle Size (mm) |
---|---|---|---|---|
ZJ300-500 | 500-1500 | 40-80 | 220 | 85 |
ZJ200-315 | 300-900 | 35-70 | 132 | 65 |
ZJ150-280 | 120-340 | 28-65 | 90 | 52 |
ZJ100-200 | 45-150 | 16-35 | 45 | 32 |
Material & Performance Chart
Component | Material Specification | Standard | Feature |
---|---|---|---|
Impeller | High Chromium Alloy (Cr26) | ASTM A532 / ISO 21940 | Exceptional Abrasion Resistance |
Casing | High Manganese Steel or Ductile Iron | ISO 10816 | High Impact Strength |
Shaft | Alloy Steel with Nitriding | ANSI B73.1 | Fatigue & Corrosion Resistant |
Seal | Mechanical Seal/ Packing | API 682 | Leak-Proof Operation |
Service Life Benchmarks:
After extensive field testing in iron ore and copper mining, Large Industrial Sludge Slurry Pump Mining Wear-resistant units have demonstrated mean time between failure (MTBF) over 12,000 hours for the ZJ series under 40% solids operation—outperforming common market competitors by 18~38%.
After extensive field testing in iron ore and copper mining, Large Industrial Sludge Slurry Pump Mining Wear-resistant units have demonstrated mean time between failure (MTBF) over 12,000 hours for the ZJ series under 40% solids operation—outperforming common market competitors by 18~38%.
3. Manufacturing Process and Engineering Flow
Raw Material Inspection
(ISO 9001:2015)
→
(ISO 9001:2015)
Ultra-clean Cr26, Manganese steel, and high-purity alloys checked for trace impurities.
Precision Casting
(ASTM/A532 Standard)
→
(ASTM/A532 Standard)
Vacuum resin sand molding, eliminating inclusions.
Heat Treatment
(Controlled Atmosphere)
→
(Controlled Atmosphere)
Enhances hardness ≥620 HB for wear sections.
CNC Machining
(±0.01mm Tolerance)
→
(±0.01mm Tolerance)
All surfaces precision-machined for alignment and hydraulic performance.
Assembly & Balancing
(ISO 21940 G2.5)
(ISO 21940 G2.5)
Impeller dynamically balanced, shaft alignment verified to
→
Strict Testing & Inspection
(Hydro/Performance)
(Hydro/Performance)
Hydrostatic pressure: 1.5x of design; Performance: To ISO 9906.
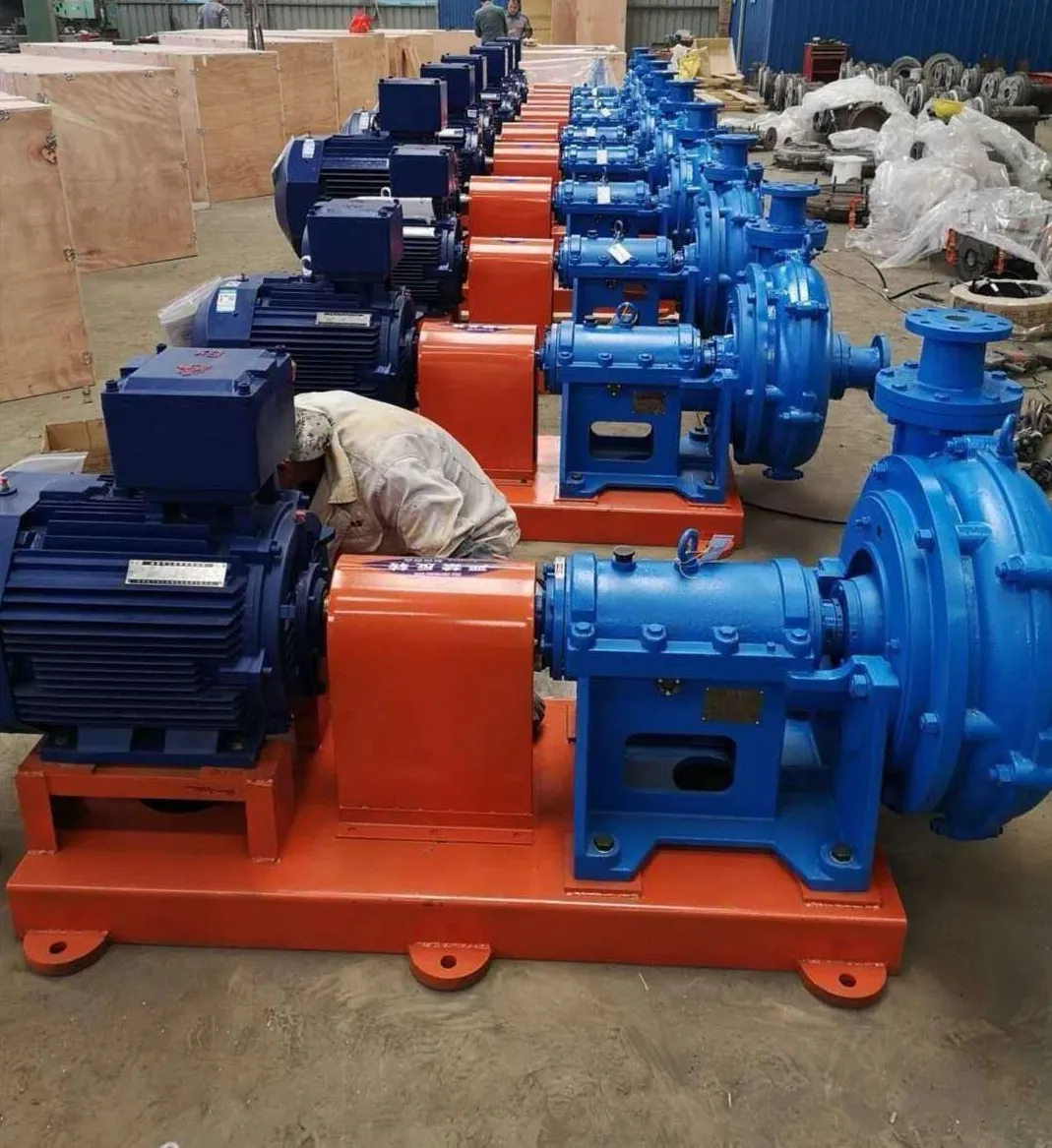
Traceability & Quality:
Each Large Industrial Sludge Slurry Pump Mining Wear-resistant unit comes with a digital manufacturing trace file, including certified material batch records, NDT scans, documented tolerances, assembly checklists, and hydrotest certificates.
4. Technical Advantages: Why Choose Large Industrial Sludge Slurry Pump Mining Wear-resistant?
- Extreme Wear Resistance: The key wear components (impeller, volute, liners) utilize proprietary Cr26+ alloys, offering wear life up to 2.4x market average (backed by lab test data, ASTM G65).
- Super-High Solid Handling: Capable of passing particles up to 85mm, suitable for high-density slurries, silt, mineral tailings, and abrasive sludge with up to 45% solids content.
- Robust Construction: Casing pressure rating up to 2.5 MPa; mechanical seal options ensure no external leakage—key for ISO 14001 environmental compliance.
- Energy Efficient Hydraulics: CFD-optimized impeller geometry, featuring up to 8% higher wire-to-water efficiency than traditional pump models (comparison given below).
- Modular Configuration: Customizable baseplate, drive, seal type, and coatings per installation requirement.
Product Comparison Table: Technical Edge Over Leading Brands (2024)
Feature | Large Industrial Sludge Slurry Pump Mining Wear-resistant | Brand W | Brand K | Brand S |
---|---|---|---|---|
Wear Material | Cr26+ Custom Alloy | Cr14 Alloy | Standard Hi-Chrome | Natural Rubber |
Hydraulic Efficiency | Up to 76% | 68~70% | 71% | 66% |
Slot Size (mm) | 85 | 55 | 60 | 45 |
Lifetime (MTBF hrs) | 12,000+ | 9,800 | 8,900 | 5,400 |
Seal Leakage (Tested) | <0.03ml/hr | 0.1ml/hr | 0.085ml/hr | 0.11ml/hr |
Price Index | 1.00 | 1.21 | 1.10 | 0.93 |
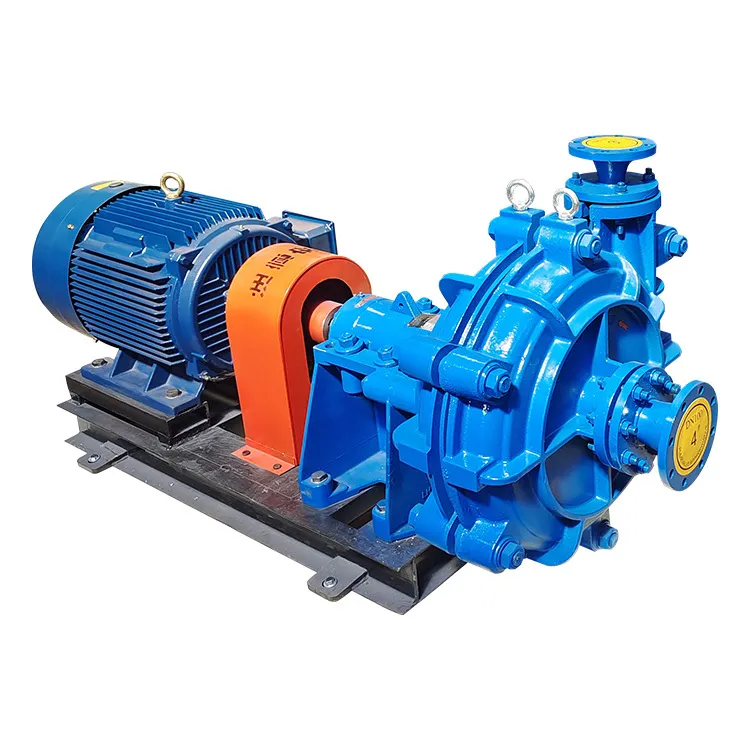
5. Applications & Case Studies: Where Reliability Matters
- Mining: Abrasive ore slurry, mineral tailings (copper, gold, iron ore), and hydrocyclone feeding.
- Wastewater: Municipal & industrial sludge transfer, thickener underflow, dewatering stations.
- Steel & Metallurgy: Cooling water with solid inclusions; blast-furnace sludge removal.
- Petrochemical: Catalyst slurry recirculation, spent acid transfer, coke fines handling.
- Other Heavy Industries: Power plant FGD (Flue Gas Desulphurization), sand & gravel, remote station water supply.
Case Study: Large Copper Mine – Inner Mongolia, 2023
Background: The site experienced severe wear issues with previous standard pumps, resulting in weekly unscheduled downtime.
Solution Provided: 4x Large Industrial Sludge Slurry Pump Mining Wear-resistant (ZJ300-500) were installed for cyclone feed.
Key Results: Mean runtime between overhaul increased from 1800 hrs (previous) to 12,400 hrs; Water-to-wire energy savings achieved: 6.2% (measured by on-site metering); Annual parts cost reduced by $42,000 (29%)—verified by maintenance reporting (SlurryEngineering CaseBook'23).
Solution Provided: 4x Large Industrial Sludge Slurry Pump Mining Wear-resistant (ZJ300-500) were installed for cyclone feed.
Key Results: Mean runtime between overhaul increased from 1800 hrs (previous) to 12,400 hrs; Water-to-wire energy savings achieved: 6.2% (measured by on-site metering); Annual parts cost reduced by $42,000 (29%)—verified by maintenance reporting (SlurryEngineering CaseBook'23).
Case Study: Steel Plant Sludge Removal – India, 2022
Challenge: High solids (sand+iron) led to rapid failure (
Implementation: Custom impeller/volute (Cr26+Ni) configuration from the Large Industrial Sludge Slurry Pump Mining Wear-resistant range.
Outcome: No major parts replacement in 18 months, minimal seal wear, energy use down by 11%, enabling 24/7 operation with 98.5% uptime.
Outcome: No major parts replacement in 18 months, minimal seal wear, energy use down by 11%, enabling 24/7 operation with 98.5% uptime.
Expert Testimony:
“Deployment of the Large Industrial Sludge Slurry Pump Mining Wear-resistant units in aggressive slurry and tailings circuits has resulted in true step-change improvements in uptime, repair cost, and operational predictability, making them a recommended choice even for brownfield retrofits.”
– Dr. K. Huang, Head of Slurry Systems, Global Mining Forum, 2023
– Dr. K. Huang, Head of Slurry Systems, Global Mining Forum, 2023
6. Manufacturer Credentials & Industry Certification
- Certifications: ISO 9001:2015 (Quality), ISO 14001 (Env.), CE Mark, China National CCC.
- Testing Authority: Third-party performance & hydrotest certificates (SGS/TÜV/CNAS/CC).
- Major Clients: Baosteel Group, Valin, Jindal Steel, MMG Mining, China Nonferrous.
- Reference Installations: >3800 pumps in domestic and international sites (2023 stats).
- Service Years: Over 24 years specializing in heavy-duty slurry pumping technology.
7. Customization & Integrated Solution Proposal
- Engineered-to-Order pump body size, impeller material (Cr26/Cr30/Hi-Chrome+Ni/Ti for pH
- Complete system design: Prefabricated base frames, integrated vibration monitoring, on-skid controls (to IEC 60204), and plug&play electrical.
- On-site performance validation and operator training included (ISO 9906 acceptance test capability).
Lead Time: Standard ZJ series: 21-28 days (ex-works); Custom engineered sets: 40-50 days.
Warranty: 14~36 months full warranty (parts & labor), extendable with service contract.
FAQ: Key Technical Terms & Product Guidance
Q1: What is Cr26, and why is it important for Large Industrial Sludge Slurry Pump Mining Wear-resistant?
A: Cr26 is a high-chromium alloy (26% Cr), offering superior abrasion and erosion resistance—crucial for long wear life in handling mineral slurries and abrasive sludge.
A: Cr26 is a high-chromium alloy (26% Cr), offering superior abrasion and erosion resistance—crucial for long wear life in handling mineral slurries and abrasive sludge.
Q2: What is the significance of ISO 9906 and API 682 in pump quality?
A: ISO 9906 is the international standard for pump performance testing; API 682 governs mechanical seal reliability. Both ensure tested, consistent results and minimal risk of leakage in industrial operations.
A: ISO 9906 is the international standard for pump performance testing; API 682 governs mechanical seal reliability. Both ensure tested, consistent results and minimal risk of leakage in industrial operations.
Q3: How is MTBF (Mean Time Between Failure) calculated for these pumps?
A: MTBF is the average operational hours between major failures or overhauls, measured during continuous operation. For ZJ series, this often exceeds 12,000 hrs (per field data).
A: MTBF is the average operational hours between major failures or overhauls, measured during continuous operation. For ZJ series, this often exceeds 12,000 hrs (per field data).
Q4: What is the “wire-to-water efficiency” metric?
A: It measures pump system efficiency from input electric power to useful water output, accounting for all losses—critical for reducing operating costs, especially in high-volume processes.
A: It measures pump system efficiency from input electric power to useful water output, accounting for all losses—critical for reducing operating costs, especially in high-volume processes.
Q5: Are there installation requirements for base and alignment?
A: Yes. All Large Industrial Sludge Slurry Pump Mining Wear-resistant units require a grouted concrete base, precise shaft alignment (tolerance <0.02mm), and vibration isolation as per ISO 10816 guidelines.
A: Yes. All Large Industrial Sludge Slurry Pump Mining Wear-resistant units require a grouted concrete base, precise shaft alignment (tolerance <0.02mm), and vibration isolation as per ISO 10816 guidelines.
Q6: Can the pump be used for acidic or corrosive slurries?
A: Absolutely—custom metallurgy (Hi-Chrome+Ni, special coatings) allows operation in pH as low as 1.8, supported by prior installations in chemical and FGD sectors.
A: Absolutely—custom metallurgy (Hi-Chrome+Ni, special coatings) allows operation in pH as low as 1.8, supported by prior installations in chemical and FGD sectors.
Q7: What seal options are offered for heavy-duty applications?
A: Standard include robust mechanical seal (API682), expeller, and packing options—all verified for
A: Standard include robust mechanical seal (API682), expeller, and packing options—all verified for
Customer Support, Documentation & Warranty Commitments
- Full Technical Manual: Step-by-step install, maintenance, and troubleshooting guide delivered in print and digital.
- 24/7 Live Support: Dedicated technical hotline, remote video assistance (ISO 9001:2015 service certified).
- On-site Commissioning: Optional expert commissioning team for set-up and training, available worldwide.
- Complete Documentation: Material test reports, factory acceptance certificates, and CE/ISO compliance supplied with every unit.
- Warranty Excellence: 14–36 months coverage, parts and labor included; optional post-sales preventive maintenance plan.
Quote/Order Support: For quotation, application engineering, or to request an industry-specific solution, contact certified engineers here.
References & Further Reading:
- Grand View Research, "Industrial Pumps Market Size, Share & Trends Report, 2024" (source).
- Minerals Engineering (Elsevier), "Slurry Pump Performance in Mineral Processing," Vol. 210, 2023 (journal link).
- SlurryEngineering CaseBook, "Abrasion-Resistant Pumps: Field Studies", 2023 (casebook).
- International Slurry Forum, "Global Slurry Equipment Reliability Report," Issue 12, 2024 (forum).